A concrete anti-crack and anti-seepage admixture and preparation method thereof
A concrete and admixture technology, applied in the field of inorganic material processing, can solve the problems of high fly ash loss on ignition, affect water seepage effect, inconvenient use, etc., achieve less environmental pollution, lower production cost, increase compactness and The effect of abrasion resistance
- Summary
- Abstract
- Description
- Claims
- Application Information
AI Technical Summary
Problems solved by technology
Method used
Image
Examples
Embodiment 1
[0017] A concrete anti-cracking and anti-seepage admixture, its preparation method is as follows:
[0018] 1) Weigh each raw material component according to the following proportions: 0.9% of ammonium pentaborate, 6% of polyaluminum sulfate, 3% of ammonium sulfate, 3% of potassium oleate, and 87.1% of water;
[0019] 2) Add ammonium pentaborate and water to the reaction kettle, stir at room temperature for 10 minutes (the stirring speed is 60r / min throughout the process), then add polyaluminum sulfate and stir for 10 minutes, then add ammonium sulfate, and keep stirring at 40°C After 15 minutes, add potassium oleate at last, stop heating after stirring for 85 minutes, and cool to room temperature to obtain concrete anti-cracking and anti-seepage admixture.
Embodiment 2
[0021] A concrete anti-cracking and anti-seepage admixture, its preparation method is as follows:
[0022] 1) Weigh each raw material component according to the following ratio: ammonium pentaborate 0.7%, polyaluminum sulfate 8.8%, ammonium sulfate 3.8%, potassium oleate 3%, water 83.7%;
[0023] 2) Add ammonium pentaborate and water to the reactor, stir at room temperature for 15 minutes, then add polyaluminum sulfate and stir for 25 minutes, then add ammonium sulfate, keep stirring at 45°C for 15 minutes, finally add potassium oleate, and stir for 65 minutes Finally, stop heating and cool to room temperature to obtain the concrete anti-crack and anti-seepage admixture.
Embodiment 3
[0025] A concrete anti-cracking and anti-seepage admixture, the preparation method is as follows:
[0026] 1) Weigh each raw material component according to the following proportions: 0.6% of ammonium pentaborate, 3% of polyaluminum sulfate, 5% of ammonium sulfate, 5% of potassium oleate, and 86.4% of water;
[0027] 2) Add ammonium pentaborate and water to the reactor, stir at room temperature for 15 minutes, then add polyaluminum sulfate and stir for 15 minutes, then add ammonium sulfate, keep the temperature at 30°C and stir for 20 minutes, finally add potassium oleate, stir for 70 After 10 minutes, stop heating and cool to room temperature to obtain the concrete anti-crack and anti-seepage admixture.
PUM
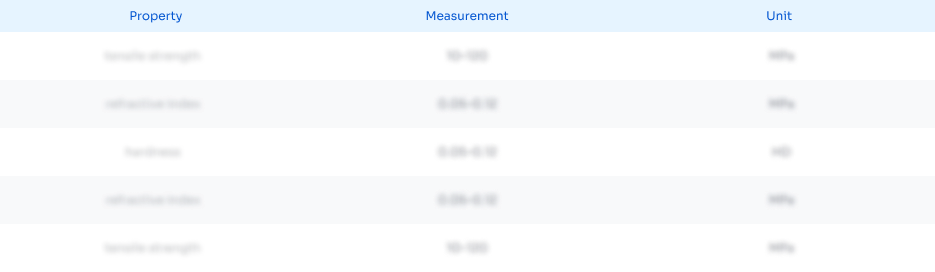
Abstract
Description
Claims
Application Information

- Generate Ideas
- Intellectual Property
- Life Sciences
- Materials
- Tech Scout
- Unparalleled Data Quality
- Higher Quality Content
- 60% Fewer Hallucinations
Browse by: Latest US Patents, China's latest patents, Technical Efficacy Thesaurus, Application Domain, Technology Topic, Popular Technical Reports.
© 2025 PatSnap. All rights reserved.Legal|Privacy policy|Modern Slavery Act Transparency Statement|Sitemap|About US| Contact US: help@patsnap.com