Phenolic resin composite board and preparation method thereof
A technology of phenolic resin and composite board, applied in the field of phenolic resin materials, can solve problems such as short service life, influence on popularization and application, and potential safety hazards
- Summary
- Abstract
- Description
- Claims
- Application Information
AI Technical Summary
Problems solved by technology
Method used
Image
Examples
preparation example Construction
[0039] Based on the same inventive concept, an embodiment of the present application further provides a method for preparing the phenol resin of the composite sheet, comprising the steps of:
[0040] S1, formulated expandable phenolic resin material;
[0041] S2, providing a mold, the foamable phenolic resin material plated in a mold, and then placed on the corrugated plate can be made of phenolic resin materials, can be made and then added to the phenolic resin material corrugated board surface, and then be Add the hair phenolic resin corrugated board material, and then added to the surface of the corrugated plate can be made of phenol resin materials, followed by cycle;
[0042] S3, after the mold is closed, foaming phenol resin to obtain the composite sheet.
[0043] Incidentally, the phenol resin prepared in Example of the present application embodiment of the composite sheet, first formulated expandable phenolic resin material, and then the prepared expandable phenolic resin ...
Embodiment 1
[0059] The present application example provides a method of preparing a phenolic resin composite sheet, comprising the steps of:
[0060] S1, a weight of 100 parts of a thermosetting phenolic resin liquid, 12 parts of surfactant Tween 80, 15 parts of a foam nanopentane, 8 parts of nitric nitric acid stirred at room temperature for 5 min, resulting in hairability Phenolic resin;
[0061] S2, a mold is provided, tabulated in the mold in the mold, and then places the corrugated phenolic resin, and then add a privylene phenol resin surface on the surface of the corrugated plate;
[0062] S3, after the mold is molded, foamed at 80 ° C for 3 h, that is, the phenolic resin foam composite sheet;
[0063] Among them, the corrugated plate is a composite material with a phenolic resin as a substrate, a composite material of a glass fiber cloth, which is prepared by placing two-layer glass fibers together, wetting the phenolic resin, on the hot press on 120 Heating at ° C, after 15 min, the p...
Embodiment 2
[0068] The present application provides a method of preparing a phenolic resin composite sheet, in the same embodiment, and different in that step S2 is specifically: providing a mold, laying the hairdable phenolic resin is tangled in the mold, and then the corrugation plate is placed The proconsive phenol resin is added to the surface of the zigzags and then placed on the surface of the corrugated plate, and a layer of corrugated plate is added thereto, and the viscular phenolic resin is added to the surface of the corrugated plate. In this embodiment, two layers of corrugated plates, the ridge direction of the corrugated plate is parallel to each other, specifically, the stacking method is specifically figure 1 As shown, the corrugated sheet is made of the corrugated plate prepared in Example 1 in the present application embodiment.
PUM
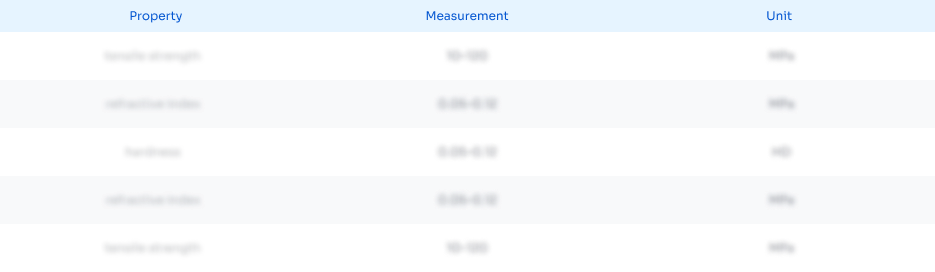
Abstract
Description
Claims
Application Information

- R&D
- Intellectual Property
- Life Sciences
- Materials
- Tech Scout
- Unparalleled Data Quality
- Higher Quality Content
- 60% Fewer Hallucinations
Browse by: Latest US Patents, China's latest patents, Technical Efficacy Thesaurus, Application Domain, Technology Topic, Popular Technical Reports.
© 2025 PatSnap. All rights reserved.Legal|Privacy policy|Modern Slavery Act Transparency Statement|Sitemap|About US| Contact US: help@patsnap.com