Chip mounter suction nozzle coaxiality error automatic calibration method based on machine vision
A machine vision, automatic calibration technology, applied in the direction of electrical components, electrical components, electrical components assembling printed circuits, etc., can solve problems such as difficulty in ensuring consistency, affecting placement accuracy, and changes in mechanical positioning accuracy.
- Summary
- Abstract
- Description
- Claims
- Application Information
AI Technical Summary
Problems solved by technology
Method used
Image
Examples
Embodiment Construction
[0024] In order to make the technical problems, technical solutions and beneficial effects solved by the present invention clearer, the present invention will be further described in detail below in conjunction with the accompanying drawings and embodiments. It should be understood that the specific embodiments described here are only used to explain the present invention, not to limit the present invention.
[0025] See figure 1 , a method for automatic calibration of the coaxiality error of the chip mounter nozzle based on machine vision of the present invention, the specific steps are as follows:
[0026] Step 1. First, perform a mechanical return to zero on the rotation axis of the suction nozzle on the placement head, and ensure that this position is used as a reference point for compensation every time. The role of the rotary axis of the suction nozzle is illustrated as an example. The suction nozzle picks up the workpiece and corrects the angular deviation between the ...
PUM
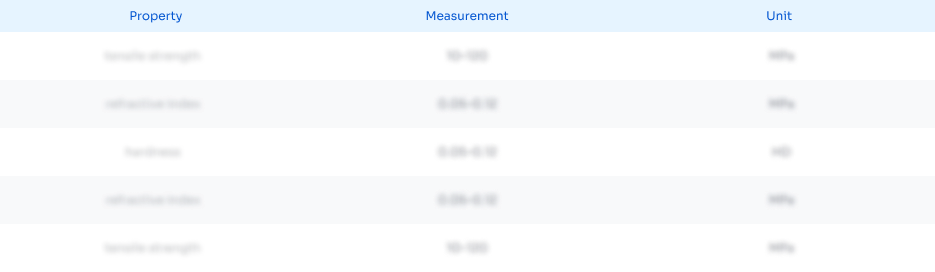
Abstract
Description
Claims
Application Information

- Generate Ideas
- Intellectual Property
- Life Sciences
- Materials
- Tech Scout
- Unparalleled Data Quality
- Higher Quality Content
- 60% Fewer Hallucinations
Browse by: Latest US Patents, China's latest patents, Technical Efficacy Thesaurus, Application Domain, Technology Topic, Popular Technical Reports.
© 2025 PatSnap. All rights reserved.Legal|Privacy policy|Modern Slavery Act Transparency Statement|Sitemap|About US| Contact US: help@patsnap.com