Biomass fuel and production process thereof
A technology of biomass fuel and production process, applied in the direction of biofuel, waste fuel, fuel, etc., can solve the problems of high slagging rate, insufficient combustion, low calorific value, etc.
- Summary
- Abstract
- Description
- Claims
- Application Information
AI Technical Summary
Problems solved by technology
Method used
Image
Examples
Embodiment 1
[0054] A production process of biomass fuel, consisting of the following steps:
[0055] Z1 crushes crop straw residues and dries them to obtain residue powder;
[0056] Z2 Mix the residue powder and anti-slagging agent, then press and cut to obtain granular biomass fuel.
[0057] In the Z1 process: the crop stalk residue is a mixture of bagasse, sorghum stalk, cassava residue, and corn stalk in a mass ratio of 1:1:1:1; the drying temperature is 75°C, and the drying time is 3h; the fiber length of the residue powder is ≤7mm.
[0058] In the Z2 process: the mass ratio of the residue powder to the anti-slagging agent is 19:1; the pressure of the pressing is 13MPa, and the holding time is 35min; the size of the biomass fuel is 2mm×2mm× 2mm.
[0059] The preparation method of described anti-slagging agent is:
[0060] E1 adopts two sizes of alumina grinding balls to dry-grind the ore through a planetary ball mill to obtain ore powder;
[0061] E2 washes the ore powder obtaine...
Embodiment 2
[0069] It is basically the same as Example 1, except that the wetting agent is polyoxyethylene sorbitan laurate.
Embodiment 3
[0071] It is basically the same as Example 1, except that the wetting agent is polyethylene glycol diacrylate.
PUM
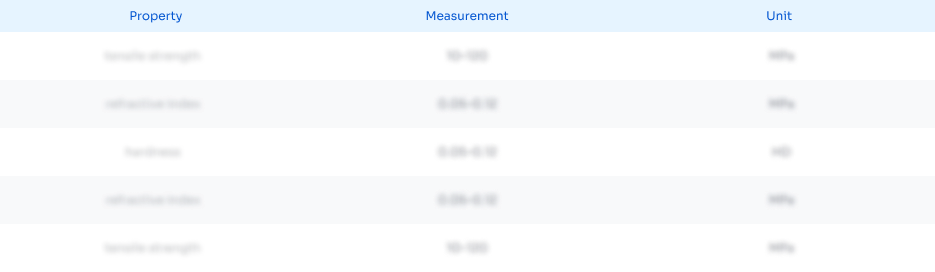
Abstract
Description
Claims
Application Information

- R&D
- Intellectual Property
- Life Sciences
- Materials
- Tech Scout
- Unparalleled Data Quality
- Higher Quality Content
- 60% Fewer Hallucinations
Browse by: Latest US Patents, China's latest patents, Technical Efficacy Thesaurus, Application Domain, Technology Topic, Popular Technical Reports.
© 2025 PatSnap. All rights reserved.Legal|Privacy policy|Modern Slavery Act Transparency Statement|Sitemap|About US| Contact US: help@patsnap.com