Efficient curing transfer printing digital roller printing process and equipment
A kind of printing equipment and digital technology, applied in transfer printing, rotary printing machine, printing, etc., can solve the problems affecting printing efficiency and so on
- Summary
- Abstract
- Description
- Claims
- Application Information
AI Technical Summary
Problems solved by technology
Method used
Image
Examples
Embodiment 1
[0036] refer to figure 1 , a high-efficiency curing transfer digital roller printing process, comprising the following steps:
[0037] a. Spray the antistatic release ink on the printing roller 1 according to the set position and perform pre-light curing treatment. The pre-light curing treatment adopts ultraviolet light with an intensity of 90W / cm and a wavelength of 313nm for 0.1-0.3s.
[0038] b. Before embossing, the substrate runs close to the pinch roller 2 for a certain distance, and the substrate is preheated by heating the pinch roller 2 . The preheating temperature of the preheating treatment is 90-120°C, so that the antistatic release ink has a certain viscosity on the bonding surface of the substrate, and is transferred to the preheated substrate under the action of pressure.
[0039] c. The substrate preheated in step b is sent between the printing roller 1 and the pressure roller 2, and the antistatic release ink after the pre-light curing treatment in step a is...
Embodiment 2
[0046] This embodiment is basically the same as Example 1, except that the antistatic release ink consists of 10 parts of pigment red, 30 parts of polyurethane, 8 parts of rosin modified phenolic resin, 3 parts of trimethylolpropane trimethylolpropane in parts by weight. Palm kernel ester, 2 parts of paraffin micropowder, 2 parts of polytetrafluoroethylene micropowder, 1 part of salmon cartilage powder, 1 part of photoinitiator, 2 parts of antistatic agent, 0.3 part of defoamer and 40.7 parts of solvent are mixed and ground to 30nm .
[0047] Among them, the photoinitiator is compounded with photoinitiator 907, photoinitiator DETX and photoinitiator ITX in a weight ratio of 3:2:2.
Embodiment 3
[0049]This embodiment is basically the same as Example 1, except that the antistatic release ink consists of 9 parts of pigment yellow, 32 parts of polyurethane, 4 parts of rosin modified phenolic resin, and 5 parts of trimethylolpropane trimethylolpropane in parts by weight. Palm kernel ester, 2 parts of paraffin micropowder, 2 parts of polytetrafluoroethylene micropowder, 1 part of salmon cartilage powder, 2 parts of photoinitiator, 1 part of antistatic agent, 0.4 part of defoamer and 41.6 parts of solvent are mixed and ground to 40nm .
[0050] Among them, the photoinitiator is compounded with photoinitiator 819, photoinitiator DETX, and photoinitiator ITX in a weight ratio of 3:2:1.
PUM
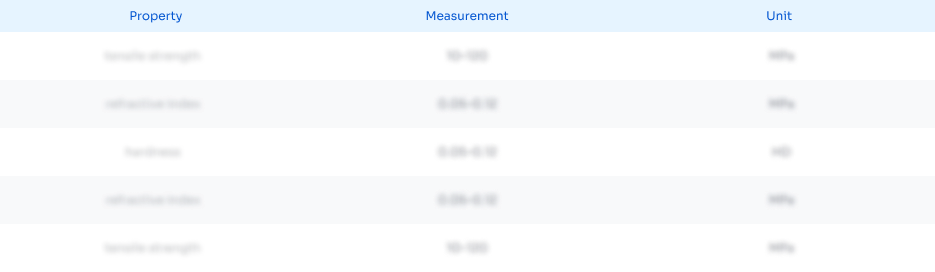
Abstract
Description
Claims
Application Information

- Generate Ideas
- Intellectual Property
- Life Sciences
- Materials
- Tech Scout
- Unparalleled Data Quality
- Higher Quality Content
- 60% Fewer Hallucinations
Browse by: Latest US Patents, China's latest patents, Technical Efficacy Thesaurus, Application Domain, Technology Topic, Popular Technical Reports.
© 2025 PatSnap. All rights reserved.Legal|Privacy policy|Modern Slavery Act Transparency Statement|Sitemap|About US| Contact US: help@patsnap.com