Denitration catalyst and preparation method thereof, and waste gas denitration method
A denitration catalyst and waste gas technology, applied in chemical instruments and methods, physical/chemical process catalysts, separation methods, etc., can solve the problems of accelerated catalyst, deactivation, etc., and achieve the effect of enhancing stability, easy operation, and improving dispersion ability.
- Summary
- Abstract
- Description
- Claims
- Application Information
AI Technical Summary
Problems solved by technology
Method used
Examples
Embodiment 1
[0055] Step 1: preparing titanium nanotubes.
[0056] Take 0.83g nanometer TiO 2 Disperse in 80ml of NaOH solution with a concentration of 10mol / L, then transfer to a 100ml polytetrafluoroethylene liner and reactor, react at 130°C for 24h, and then soak the product in 500ml of hydrochloric acid solution with a concentration of 0.1mol / L , followed by washing with deionized water to pH=7, collecting by centrifugation, and drying at 80° C. for 6 hours to obtain titanium nanotubes.
[0057] Step 2: loading manganese oxide.
[0058] Disperse 1.29g of titanium nanotubes prepared in step 1 in 100ml of deionized water, and add 3.75mmol of Mn(AC) to the dispersion 2 4H 2 O and 5g of urea solid, stirred for 10min, the mixture was heated to 90°C, reacted on the reflux device for 2h, the product was washed with deionized water to pH = 7, collected by centrifugation, dried at 80°C for 6h, heated at 5°C / min, under air atmosphere , Calcined at 350°C for 2h to obtain titanium nanotubes lo...
Embodiment 2
[0065] Step 1: preparing titanium nanotubes.
[0066] Take 0.83g nanometer TiO 2 Disperse in 80ml of NaOH solution with a concentration of 10mol / L, then transfer to a 100ml polytetrafluoroethylene liner and reactor, react at 130°C for 24h, and then soak the product in 500ml of hydrochloric acid solution with a concentration of 0.1mol / L , followed by washing with deionized water to pH=7, collecting by centrifugation, and drying at 80° C. for 6 hours to obtain titanium nanotubes.
[0067] Step 2: loading manganese oxide.
[0068] Disperse 1.29g of titanium nanotubes prepared in step 1 in 100ml of deionized water, and add 3.75mmol of Mn(AC) to the dispersion 2 4H 2 O and 5g of urea solid, stirred for 10min, the mixture was heated to 90°C, reacted on the reflux device for 2h, the product was washed with deionized water to pH = 7, collected by centrifugation, dried at 80°C for 6h, heated at 5°C / min, under air atmosphere , Calcined at 350°C for 2h to obtain titanium nanotubes lo...
Embodiment 3
[0075] Step 1: preparing titanium nanotubes.
[0076] Take 0.83g nanometer TiO 2 Disperse in 80ml of NaOH solution with a concentration of 10mol / L, then transfer to a 100ml polytetrafluoroethylene liner and reactor, react at 130°C for 24h, and then soak the product in 500ml of hydrochloric acid solution with a concentration of 0.1mol / L , followed by washing with deionized water to pH=7, collecting by centrifugation, and drying at 80° C. for 6 hours to obtain titanium nanotubes.
[0077] Step 2: loading manganese oxide.
[0078] Disperse 1.29g of titanium nanotubes prepared in step 1 in 100ml of deionized water, and add 3.75mmol of Mn(AC) to the dispersion 2 4H 2 O and 5g of urea solid, stirred for 10min, the mixture was heated to 90°C, reacted on the reflux device for 2h, the product was washed with deionized water to pH = 7, collected by centrifugation, dried at 80°C for 6h, heated at 5°C / min, under air atmosphere , Calcined at 350°C for 2h to obtain titanium nanotubes lo...
PUM
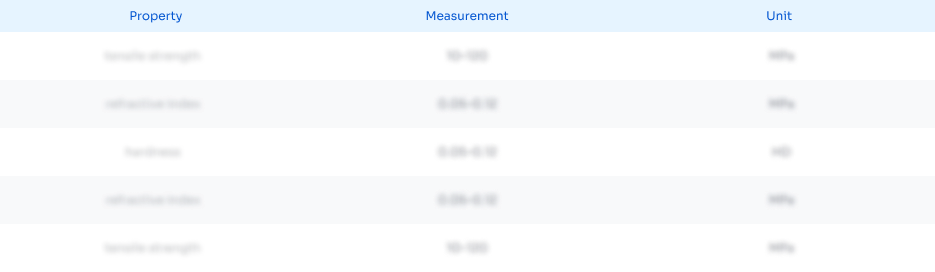
Abstract
Description
Claims
Application Information

- R&D
- Intellectual Property
- Life Sciences
- Materials
- Tech Scout
- Unparalleled Data Quality
- Higher Quality Content
- 60% Fewer Hallucinations
Browse by: Latest US Patents, China's latest patents, Technical Efficacy Thesaurus, Application Domain, Technology Topic, Popular Technical Reports.
© 2025 PatSnap. All rights reserved.Legal|Privacy policy|Modern Slavery Act Transparency Statement|Sitemap|About US| Contact US: help@patsnap.com