LED lamp circuit board welding process applying LLC series resonance circuit
A series resonant circuit, LED lamp technology, applied in the direction of assembling printed circuits with electrical components, printed circuits, printed circuit manufacturing, etc., can solve the problem of difficult collection of insulating layers, etc.
- Summary
- Abstract
- Description
- Claims
- Application Information
AI Technical Summary
Problems solved by technology
Method used
Image
Examples
Embodiment 1
[0061] Such as figure 1 As shown, a circuit board welding process for LED lights using an LLC series resonant circuit includes the following steps:
[0062] Step 1: Wire splitting, the wire feeding device 3 is sent to cooperate with the wire block mechanism 413, and the wire driving mechanism 411 drives the wire block mechanism 413 to move down to separate the wires separately;
[0063] Step 2: cutting the insulation layer. After step 1, the power assembly 422 drives the wire block mechanism 413 to move laterally, and then straightens the wire, and then the cutting assembly 421 cuts the insulation layer of the wire. At the same time, several groups of round rollers 4216 will The cut insulation is fixed;
[0064] Step 3: peeling, after step 2, the power assembly 422 continues to drive the wire block mechanism 413 to move laterally, the cutting assembly 421 removes the insulating layer, and at the same time, the smearing unit 4214 applies solder paste to the inner core of the w...
Embodiment 2
[0077] Such as figure 2 As shown, a circuit board welding process for LED lamps using an LLC series resonant circuit, including conveying equipment for conveying PCB boards, welding equipment arranged directly above the conveying equipment, and located on the left and right sides of the conveying equipment Wire feeding equipment and wire stripping equipment, the wire stripping equipment includes:
[0078] A wire distribution device, the wire distribution device can be moved up and down, the wire distribution device is provided with an accommodation chamber, and the accommodation chamber separates the wires separately;
[0079] A peeling device, the peeling device includes a cutting assembly located around the accommodating cavity and used to cut the wire insulation, a power assembly that drives the cutting assembly to move laterally to remove the insulation sheet, and drives the insulation to move A control assembly that rotates in the center and collects loose insulation. ...
PUM
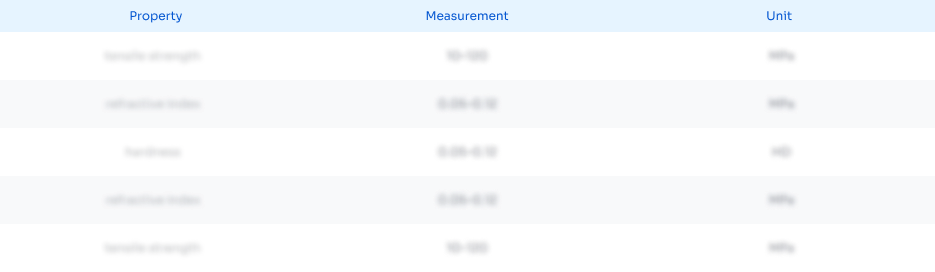
Abstract
Description
Claims
Application Information

- R&D Engineer
- R&D Manager
- IP Professional
- Industry Leading Data Capabilities
- Powerful AI technology
- Patent DNA Extraction
Browse by: Latest US Patents, China's latest patents, Technical Efficacy Thesaurus, Application Domain, Technology Topic, Popular Technical Reports.
© 2024 PatSnap. All rights reserved.Legal|Privacy policy|Modern Slavery Act Transparency Statement|Sitemap|About US| Contact US: help@patsnap.com