Forming method of block stator, block stator and motor under full-scale control
A full-size, stator technology, applied in the manufacture of stator/rotor bodies, manufacturing tools, electric components, etc., can solve the problems of motor stator and rotor iron cores that cannot be aligned, and achieve the effects of saving the number of tooling, reliable forming, and easy switching of tooling
- Summary
- Abstract
- Description
- Claims
- Application Information
AI Technical Summary
Problems solved by technology
Method used
Image
Examples
Embodiment 1
[0064] A method for forming a segmented stator under full-scale control, which includes a set of the same tooling used in the two processes of forming and welding a stator core and a method of using the same, as follows:
[0065] The tooling includes a mandrel, a notch positioning rod, a toothed positioning rod, an upper pressure plate, a lower pressure plate, a screw and an outer circle fixing hoop. The outer circle fixing hoop is composed of three parts: upper, middle and lower. The circular fixing hoop only uses the upper and lower parts. In the stator core welding process, the outer circular fixing hoop uses the upper, middle and lower parts.
[0066] Press the notch positioning rod into the mandrel, and then match the two with the inner circle part of the lower pressing plate; then insert the toothed positioning rod into the corresponding position of the lower pressing plate.
[0067] Put the laminated stator core into the position corresponding to the tooling in step 2. ...
Embodiment 2
[0074] The invention discloses a method for iron core shaping, which realizes full-scale control of the shape and position tolerance of the iron core through the cooperation of the stator iron core after lamination and the various parts of the tooling.
[0075] The method of lamination and shaping of the stator core, through the cooperation of V-shaped buckle and tooling, is used to set the size, which is convenient for the installation of the skeleton, and can ensure that the size error of the core meets the expected requirements after the stator winding is completed.
[0076] One set of tooling is used for two processes. Among them, the outer circle positioning hoop of tooling 5 adopts a three-section block structure. During the iron core shaping process, only the two sections 5-1 and 5-3 in the outer circle positioning hoop of tooling 5 are used. The full-size positioning of several iron core blocks can be achieved by cooperating with other parts of the tooling, and the V-sh...
PUM
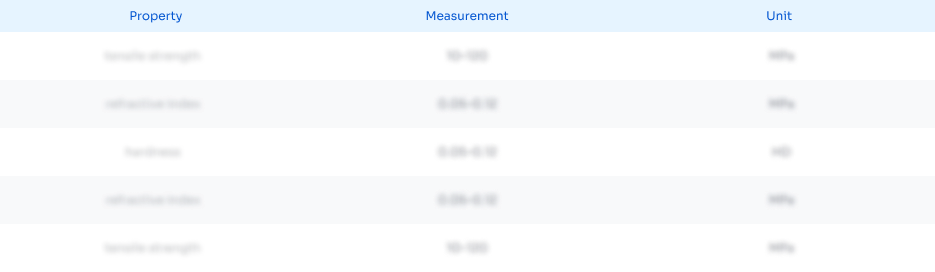
Abstract
Description
Claims
Application Information

- R&D
- Intellectual Property
- Life Sciences
- Materials
- Tech Scout
- Unparalleled Data Quality
- Higher Quality Content
- 60% Fewer Hallucinations
Browse by: Latest US Patents, China's latest patents, Technical Efficacy Thesaurus, Application Domain, Technology Topic, Popular Technical Reports.
© 2025 PatSnap. All rights reserved.Legal|Privacy policy|Modern Slavery Act Transparency Statement|Sitemap|About US| Contact US: help@patsnap.com