Production equipment and method for dovetail-type high-strength, high-conductivity, wear-resistant copper-steel composite contact wire
A technology of composite contact and production equipment, applied in the field of wire rods, can solve the problems of limited improvement, large wear, shortened service life of contact wires, etc.
- Summary
- Abstract
- Description
- Claims
- Application Information
AI Technical Summary
Problems solved by technology
Method used
Image
Examples
Embodiment 1
[0033] see Figure 1-3 , figure 1 A schematic diagram of the production equipment for a dovetail-shaped high-strength, high-conductivity and wear-resistant copper-steel composite contact wire is drawn. As shown in the figure, the production equipment of the dovetail type high-strength, high-conductivity and wear-resistant copper-steel composite contact wire involved in the present invention includes a first mold 4, a second mold 6 and a finishing mold 9 arranged in sequence, and the first mold 4 includes The injection section and the cooling section, the injection section is provided with three injection ports, inject copper water 1, copper-magnesium alloy furnace water 2 and molten steel 3 respectively, the cooling section is provided with a first circulating cooling system 5, and the second mold 6 includes injection Section and cooling section, the injection section is provided with an injection port, injects copper-steel mixed furnace water 7, and the cooling section is pr...
PUM
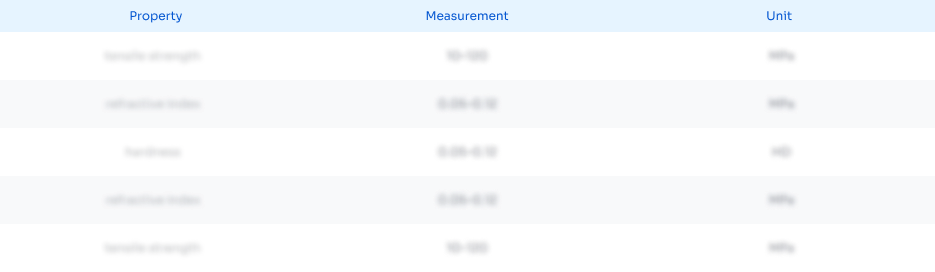
Abstract
Description
Claims
Application Information

- R&D Engineer
- R&D Manager
- IP Professional
- Industry Leading Data Capabilities
- Powerful AI technology
- Patent DNA Extraction
Browse by: Latest US Patents, China's latest patents, Technical Efficacy Thesaurus, Application Domain, Technology Topic, Popular Technical Reports.
© 2024 PatSnap. All rights reserved.Legal|Privacy policy|Modern Slavery Act Transparency Statement|Sitemap|About US| Contact US: help@patsnap.com