Method and equipment for preparing ethylene oxide from high-concentration chloroethanol
A technology of ethylene oxide and chloroethanol, applied in separation methods, chemical instruments and methods, distillation separation, etc., can solve the problems of large amount of sewage, large investment, non-compliance, etc., and achieve the effect of less pollution
- Summary
- Abstract
- Description
- Claims
- Application Information
AI Technical Summary
Problems solved by technology
Method used
Image
Examples
Embodiment 1
[0044] Embodiment 1 uses 1.7m 3 / h mass concentration is 50% chloroethanol solution and 15m 3 / h mass concentration of 9.48% milk of lime solution preheated to 80 ℃, into the pre-reactor (converted to chloroethanol and milk of lime solution in the molar ratio of calcium hydroxide is 0.6). The residence time of the material in the pre-reactor is about 2-3 seconds, and it enters a saponification reaction rectification tower with a diameter of 800 mm and a total of 17 plates. The position of the feeding plate is the sixth, and the condensation temperature of the top part of the tower is 40 ° C. , the reflux volume is 2m 3 / h (the condensate after the top part of the tower is condensed is full reflux, and the uncondensed part is the product ethylene oxide), the amount of the top product is 0.6m 3 / h, wherein the content of ethylene oxide is 77.47% (wt), the content of chloroethanol is 0.55% (wt), the temperature at the bottom of the tower is 101-102°C, and the temperature at the...
Embodiment 2
[0047] Embodiment 2 uses 1.7m 3 / h mass concentration is 60% chloroethanol solution and 18m 3 / h The milk of lime with a mass concentration of 9.48% is preheated to 75° C. and enters the prereactor (the molar ratio of chloroethanol to calcium hydroxide in the milk of lime solution is 0.6). The residence time of the material in the pre-reactor is about 2-3 seconds, and it enters a saponification reaction rectification tower with a diameter of 1000 mm and a total of 17 plates. The position of the feeding plate is the sixth, and the condensation temperature of the top part of the tower is 30 ° C. , the reflux volume is 2.4m 3 / h, the amount of product at the top of the tower is 0.72m 3 / h, wherein the ethylene oxide content is 77.75% (wt), the chlorohydrin content is 0.45% (wt), the temperature at the bottom of the tower is 101-102°C, and the temperature at the top of the tower is 49°C. The pressure at the bottom of the tower is a gauge pressure of 15kPa, and the pressure at th...
Embodiment 3
[0050] Embodiment 3 uses 1.7m 3 / h mass concentration is 70% chloroethanol solution and 22.5m 3 / h The milk of lime with a mass concentration of 9.48% is preheated to 85°C and enters the prereactor (the molar ratio of chloroethanol to calcium hydroxide in the milk of lime solution is 0.6). The residence time of the material in the pre-reactor is about 2-3 seconds, and it enters a saponification rectification tower with a diameter of 1000 mm and a total of 17 plates. The position of the feeding plate is the sixth, and the condensation temperature of the top part of the tower is 45 ° C. , the reflux volume is 2.4m 3 / h, the amount of product at the top of the tower is 0.84m 3 / h, wherein the ethylene oxide content is 84.97% (wt), the chlorohydrin content is 0.5% (wt), the temperature at the bottom of the tower is 101-102°C, and the temperature at the top of the tower is 49°C. The pressure at the bottom of the tower is a gauge pressure of 12kPa, and the pressure at the top of ...
PUM
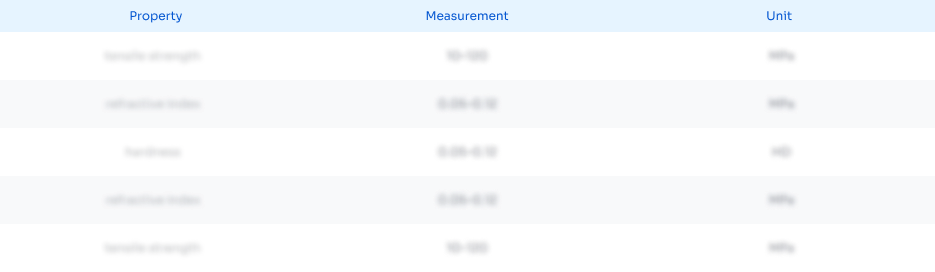
Abstract
Description
Claims
Application Information

- Generate Ideas
- Intellectual Property
- Life Sciences
- Materials
- Tech Scout
- Unparalleled Data Quality
- Higher Quality Content
- 60% Fewer Hallucinations
Browse by: Latest US Patents, China's latest patents, Technical Efficacy Thesaurus, Application Domain, Technology Topic, Popular Technical Reports.
© 2025 PatSnap. All rights reserved.Legal|Privacy policy|Modern Slavery Act Transparency Statement|Sitemap|About US| Contact US: help@patsnap.com