Co-Mo bimetallic nitride oxygen reduction catalyst as well as preparation method and application thereof
A nitride oxygen, bimetallic technology, applied in nanotechnology, structural parts, electrical components, etc. for materials and surface science, can solve problems such as being unfavorable to industrialization, and achieve considerable methanol resistance, stability, and yield. The effect of high and excellent oxygen reduction catalytic performance
- Summary
- Abstract
- Description
- Claims
- Application Information
AI Technical Summary
Problems solved by technology
Method used
Image
Examples
Embodiment 1
[0033] In the first step, weigh 0.6mmol of CoCl 2 ·6H 2 O and 0.6mmol (referring to the concentration of metal Mo ions, the same below) of H 24 Mo 7 N 6 o 24 4H 2 O was dissolved in deionized water, and then 3 mmol of urea was added, and stirred evenly at room temperature.
[0034] In the second step, the mixed solution of the first step is subjected to a hydrothermal reaction at 160±5°C. After the reaction is completed, it is lowered to room temperature, washed with water and ethanol in turn, and dried at 200°C to obtain a double metal oxide CoMoO 4 The precursor solid powder;
[0035] In the third step, the double metal oxide CoMoO 4 The precursor solid powder is placed in a magnetic boat, and the NH at 700 °C 3 Nitriding treatment under the atmosphere for 2±0.5h, and then naturally cool down to room temperature to obtain the black nitride catalytic material Co 3 Mo 3 N.
[0036] To the CoMoO obtained in the present embodiment 1 4 and Co 3 Mo 3 N conducts chara...
Embodiment 2
[0038] In the first step, weigh 0.6mmol of CoCl 2 ·6H 2 O and 0.6 mmol of H 24 Mo 7 N 6 o 24 4H 2 O was dissolved in deionized water, and then 0.6 mmol of urea was added, and stirred evenly at room temperature.
[0039] In the second step, the mixed solution of the first step is subjected to a hydrothermal reaction at 160±5°C. After the reaction is completed, it is lowered to room temperature, washed with water and ethanol in turn, and dried at 200°C to obtain a double metal oxide CoMoO 4 The precursor solid powder;
[0040] In the third step, the double metal oxide CoMoO 4 The precursor solid powder is placed in a magnetic boat, and the NH at 700 °C 3 Nitriding treatment under the atmosphere for 2±0.5h, and then naturally cool down to room temperature to obtain the black nitride catalytic material Co 3 Mo 3 N.
Embodiment 3
[0043] In the first step, weigh 0.6mmol of CoCl 2 ·6H 2 O and 0.6 mmol of H 24 Mo 7 N 6 o 24 4H 2 O was dissolved in deionized water and stirred evenly at room temperature.
[0044] In the second step, the mixed solution is subjected to a hydrothermal reaction at 160±5°C. After the reaction, it is lowered to room temperature, washed with water and ethanol in turn, and dried at 200°C to obtain a double metal oxide CoMoO 4 The precursor solid powder;
[0045] In the third step, the double metal oxide CoMoO 4 The precursor solid powder is placed in a magnetic boat, and the NH at 700 °C 3 Nitriding treatment under the atmosphere for 2±0.5h, and then naturally cool down to room temperature to obtain the black nitride catalytic material Co 3 Mo 3 N.
[0046] To the CoMoO obtained by drying treatment in the present embodiment 3 4 Conduct SEM tests such as Figure 5 As shown, when no urea is added, it is a slender rod-like morphology.
PUM
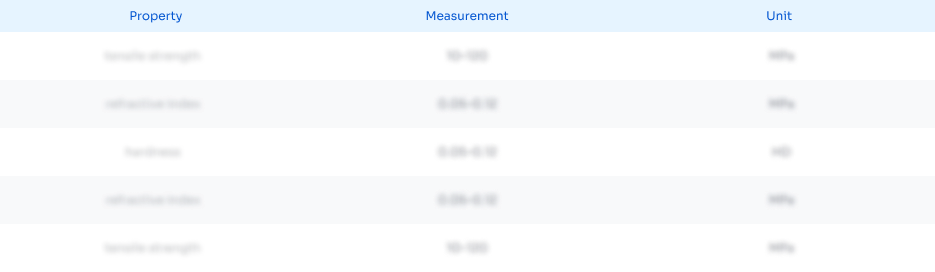
Abstract
Description
Claims
Application Information

- Generate Ideas
- Intellectual Property
- Life Sciences
- Materials
- Tech Scout
- Unparalleled Data Quality
- Higher Quality Content
- 60% Fewer Hallucinations
Browse by: Latest US Patents, China's latest patents, Technical Efficacy Thesaurus, Application Domain, Technology Topic, Popular Technical Reports.
© 2025 PatSnap. All rights reserved.Legal|Privacy policy|Modern Slavery Act Transparency Statement|Sitemap|About US| Contact US: help@patsnap.com