Thick-wall pipe lateral induction straight seam welding device and method
A technology of straight seam welding and induction heating device, applied in welding equipment, welding equipment, auxiliary equipment, etc., can solve the problem that induction heating cannot be widely used, the temperature distribution of the side wall of the weld seam is uneven, and the straight seam welding of thick-walled pipes cannot be solved. and other problems to achieve the effect of solving uneven heating, uniform heating and high heating efficiency
- Summary
- Abstract
- Description
- Claims
- Application Information
AI Technical Summary
Problems solved by technology
Method used
Image
Examples
Embodiment Construction
[0033] The following will clearly and completely describe the technical solutions in the embodiments of the present invention with reference to the drawings in the embodiments of the present invention. Based on the embodiments of the present invention, all other embodiments obtained by persons of ordinary skill in the art without making creative efforts belong to the protection scope of the present invention. It should be noted that, unless otherwise specified, the technical terms or scientific terms used in this application shall have the usual meanings understood by those skilled in the art to which the present invention belongs. For example, the terms front, back, left and right used in the present invention are merely exemplary and used for convenient description.
[0034] The technical solutions of the present invention will be further specifically described below through the embodiments and in conjunction with the accompanying drawings.
[0035] Such as Figure 1-Figur...
PUM
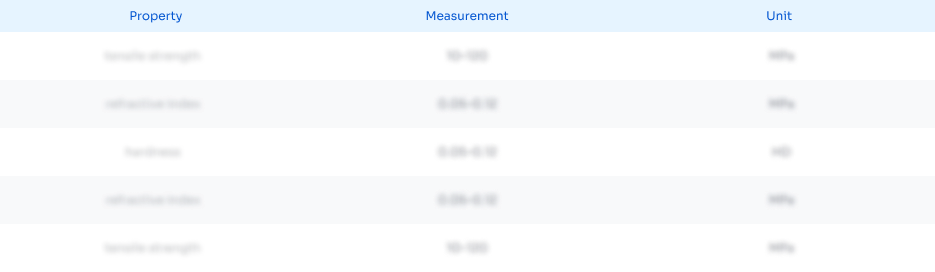
Abstract
Description
Claims
Application Information

- R&D
- Intellectual Property
- Life Sciences
- Materials
- Tech Scout
- Unparalleled Data Quality
- Higher Quality Content
- 60% Fewer Hallucinations
Browse by: Latest US Patents, China's latest patents, Technical Efficacy Thesaurus, Application Domain, Technology Topic, Popular Technical Reports.
© 2025 PatSnap. All rights reserved.Legal|Privacy policy|Modern Slavery Act Transparency Statement|Sitemap|About US| Contact US: help@patsnap.com