Preparation method and application of iron alloy catalyst
A catalyst and ferroalloy technology, which is applied in the field of ferroalloy catalyst preparation, can solve the problems of difficult treatment of coal chemical wastewater, low efficiency of organic matter, high activation energy consumption, etc., and achieve the solution of secondary pollution of heavy metals, strong applicability, and low dissolution rate Effect
- Summary
- Abstract
- Description
- Claims
- Application Information
AI Technical Summary
Problems solved by technology
Method used
Image
Examples
Embodiment 1
[0029] This embodiment provides a method for preparing a Fe-Ni-Cu / C metal catalyst, comprising the following steps;
[0030] Step 1: Fe(NO 3 ) 3 9H 2 O, Ni(NO 3 ) 3 ·6H 2 O, Cu(NO 3 ) 3 ·6H 2 O is mixed and dissolved in 100mL distilled water with a molar ratio of Fe / Ni / Cu=8:1:1, and stirred to obtain a uniform metal salt solution; It is fully impregnated, and after impregnating for 24 hours, it is dried in an oven at 80°C for 8 hours to obtain the impregnated catalyst;
[0031] Step 2: Place the impregnated catalyst in a tube furnace under N 2 / H 2 =7 / 1 under the reducing atmosphere of high-temperature calcination, the calcination temperature is 650°C, and the calcination time is 4h, and the Fe-Ni-Cu / C metal catalyst is obtained.
[0032] Using the effluent of the secondary sedimentation tank of a coking plant as the target pollutant, the degradation degree of COD of the sewage represents the treatment efficiency of organic wastewater, and the Fe-Ni-Cu / C metal catal...
Embodiment 2
[0036] This embodiment provides a method for preparing a Fe-Co-Mn / C metal catalyst, comprising the following steps;
[0037] Step 1: Fe(NO 3 ) 3 9H 2 O, Co(NO 3 ) 3 ·6H 2 O, MnCl 2 ·6H 2 O was mixed and dissolved in 100mL of distilled water at a molar ratio of Fe / Ni / Cu=10:1:5, and stirred to obtain a uniform metal salt solution; 5g of cordierite was added to the above metal salt solution, and stirred continuously at 30°C to Fully impregnated, after 14 hours of immersion, dried in an oven at 60°C for 12 hours to obtain the impregnated catalyst;
[0038] Step 2: Place the impregnated catalyst in a tube furnace under N 2 / H 2 =10 / 1 under a reducing atmosphere for high-temperature calcination, the calcination temperature is 250°C, and the calcination time is 9h, to obtain the Fe-Co-Mn / C metal catalyst.
Embodiment 3
[0040] This embodiment provides a method for preparing a Fe-Ti-Sn / C metal catalyst, comprising the following steps;
[0041] Step 1: FeCl 3 ·6H 2 O, TiCl 4 and SnCl 2 Mix and dissolve in 100mL distilled water according to the molar ratio Fe / Ti / Sn=10:1:5, and stir to obtain a uniform metal salt solution; add 8g molecular sieve ZMS-5 to the above metal salt solution, and keep stirring at 80°C to make It is fully impregnated, and after the impregnation is completed for 0.5h, it is dried in an oven at 90°C for 6h to obtain the impregnated catalyst;
[0042]Step 2: Place the impregnated catalyst in a tube furnace under N 2 / H 2 =5 / 1 under a reducing atmosphere for high-temperature calcination, the calcination temperature is 850°C, and the calcination time is 2h, to obtain the Fe-Ti-Sn / C metal catalyst.
PUM
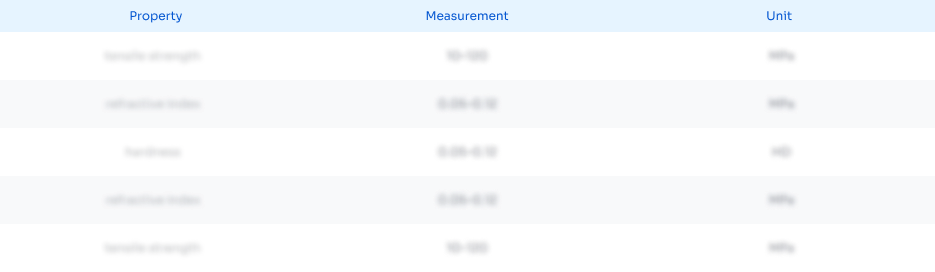
Abstract
Description
Claims
Application Information

- R&D
- Intellectual Property
- Life Sciences
- Materials
- Tech Scout
- Unparalleled Data Quality
- Higher Quality Content
- 60% Fewer Hallucinations
Browse by: Latest US Patents, China's latest patents, Technical Efficacy Thesaurus, Application Domain, Technology Topic, Popular Technical Reports.
© 2025 PatSnap. All rights reserved.Legal|Privacy policy|Modern Slavery Act Transparency Statement|Sitemap|About US| Contact US: help@patsnap.com