Polishing slurry composition for sti process
A technology of composition and slurry, which is applied in the direction of polishing composition containing abrasives, other chemical processes, water-based dispersants, etc., can solve problems such as scratches and large depression of insulating film, so as to prevent over-polishing and excellent flatness The effect of high degree and high removal speed
- Summary
- Abstract
- Description
- Claims
- Application Information
AI Technical Summary
Problems solved by technology
Method used
Image
Examples
Embodiment 1 to 7
[0082] As shown in Table 1, an additive liquid was prepared, and a polishing liquid including ceria polishing particles having a particle size of 150 nm was prepared. That is, the slurry composition for the STI polishing process was prepared at a ratio of polishing liquid: water: additive liquid of 1:6:3.
[0083] [Polishing condition]
[0084] 1. Polishing device: AP-300 (300mm, KCTECH company)
[0085] 2. Pad: IC 1000 (DOW company)
[0086] 3. Polishing time: 60 seconds
[0087] 4. Platen RPM (Platen RPM): 93rpm
[0088] 5. Spindle RPM (Spindle RPM): 87rpm
[0089] 6. Pressure: 3psi
[0090] 7. Flow rate: 250ml / min
[0091] 8. Chips used:
[0092] Wafer: PE-TEOS P-Poly
[0093] Pattern wafer: STI polysilicon pattern wafer groove depth
[0094] The polishing slurry compositions that are used for the STI process of embodiment and comparative example are shown in table 1, and the removal rate (RemovalRate : RR).
[0095] 【Table 1】
[0096]
[0097]
[...
PUM
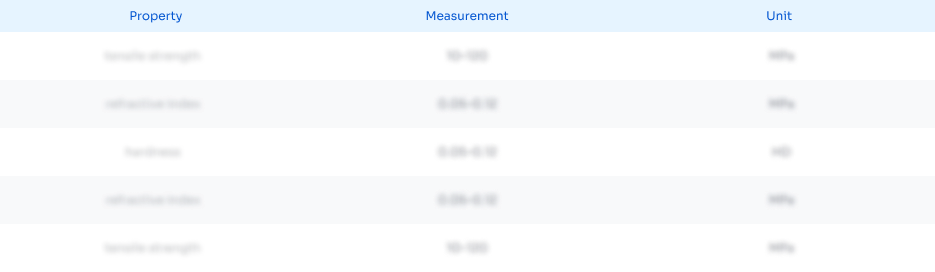
Abstract
Description
Claims
Application Information

- R&D Engineer
- R&D Manager
- IP Professional
- Industry Leading Data Capabilities
- Powerful AI technology
- Patent DNA Extraction
Browse by: Latest US Patents, China's latest patents, Technical Efficacy Thesaurus, Application Domain, Technology Topic, Popular Technical Reports.
© 2024 PatSnap. All rights reserved.Legal|Privacy policy|Modern Slavery Act Transparency Statement|Sitemap|About US| Contact US: help@patsnap.com