Plastic spraying process for cast aluminum alloy component
A technology for casting aluminum alloys and components, which is applied in the coating process of metal materials, surface pretreatment, and devices for coating liquid on the surface, etc. It can solve problems such as easy loosening and falling off, and achieve improved machinability and stable coating The effect of increased performance and reduced production cost
- Summary
- Abstract
- Description
- Claims
- Application Information
AI Technical Summary
Problems solved by technology
Method used
Image
Examples
Embodiment 1
[0032] A plastic spraying process for cast aluminum alloy components, specifically processing a cast aluminum alloy engine block (motorcycle engine block), the steps comprising:
[0033] Step 1. Shot blasting is performed on the cast aluminum alloy components. The shot blasting uses a steel shot with a particle size of 0.5 mm, model S170, and the shot blasting time is 8 minutes;
[0034] Step 2, carry out acidic degreasing treatment to the workpiece after step 1 finishes, acidic degreasing agent adopts PC-200 acidic degreasing agent (purchased from Chongqing Parn Chemical Technology Co., Ltd), the mass ratio of acidic degreasing solution is 3% (100Kg solution The quality of medium-acid degreasing agent is 3Kg), its pH value control is 2, and the temperature control in the acid degreasing process is 55 ℃, and time control is 9 minutes;
[0035] Step 3. Clean the workpiece after step 2. Specifically, wash it twice with water with pH=5, each time for 1 minute, and then wash with ...
Embodiment 2
[0047] A kind of casting aluminum alloy member (engine block) plastic spraying process, step is referred to implementation 1, and its main difference with embodiment 1 is shown in Table 3,
[0048] Casting aluminum alloy member plastic spraying process parameter in the embodiment 2 of table 3
[0049]
Embodiment 3
[0051] A kind of casting aluminum alloy member (motorcycle front bracket aluminum alloy guide rail riveted assembly) spraying process, the steps refer to implementation 1, and its main difference with embodiment 1 is shown in Table 4,
[0052] Casting aluminum alloy components spray process parameters in table 4 embodiment 3
[0053]
PUM
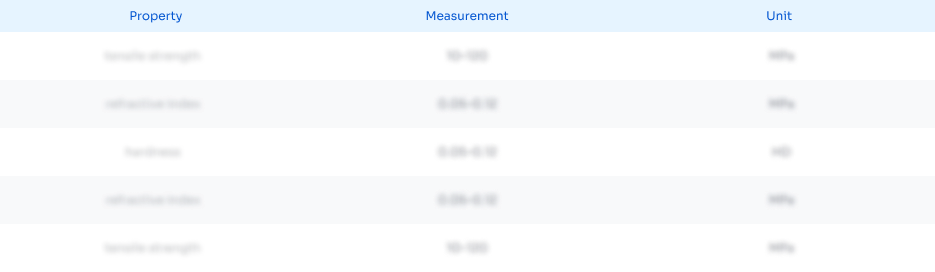
Abstract
Description
Claims
Application Information

- R&D
- Intellectual Property
- Life Sciences
- Materials
- Tech Scout
- Unparalleled Data Quality
- Higher Quality Content
- 60% Fewer Hallucinations
Browse by: Latest US Patents, China's latest patents, Technical Efficacy Thesaurus, Application Domain, Technology Topic, Popular Technical Reports.
© 2025 PatSnap. All rights reserved.Legal|Privacy policy|Modern Slavery Act Transparency Statement|Sitemap|About US| Contact US: help@patsnap.com