Composite pellet soil additive and composite pellet soil production method
An additive and composite ball technology, which is applied in the field of composite pellet soil additives and composite pellet soil production, can solve the problems of incompatibility with cost reduction, efficiency enhancement, energy conservation and environmental protection, decreased hydrophilicity of iron powder particles, and difficulty in pellet production. To achieve the effect of reasonable cost of raw materials, simple preparation method, and improved ball-forming properties
- Summary
- Abstract
- Description
- Claims
- Application Information
AI Technical Summary
Problems solved by technology
Method used
Examples
Embodiment Construction
[0011] The present invention is described in detail below.
[0012] The present invention provides a composite pelletizing soil additive and a composite pelletizing soil production method during specific implementation, including formula A and formula B, and the formula A includes 1 part of sodium lauryl sulfate, 1 part of sodium polyacrylate, 1 part of polyacrylamide, 3 parts of high viscosity CMC;
[0013] The formula B includes 1 part of sodium lauryl sulfate, 1 part of sodium polyacrylate, 1 part of polyacrylamide and 3 parts of polyvinyl alcohol.
[0014] As a further elaboration of the present invention, the following preparation steps are included:
[0015] (1) The above-mentioned raw materials are fully mixed according to standard equal parts, and set aside;
[0016] (2) Divide the water into 20-30% of the original soil, requiring the particle size to be less than 5 cm, adding 3% alkali to make it soda, and stuffing it for more than 15 days, requiring the average tem...
PUM
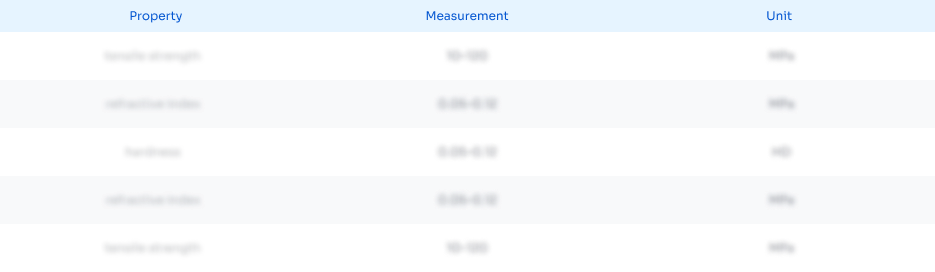
Abstract
Description
Claims
Application Information

- R&D
- Intellectual Property
- Life Sciences
- Materials
- Tech Scout
- Unparalleled Data Quality
- Higher Quality Content
- 60% Fewer Hallucinations
Browse by: Latest US Patents, China's latest patents, Technical Efficacy Thesaurus, Application Domain, Technology Topic, Popular Technical Reports.
© 2025 PatSnap. All rights reserved.Legal|Privacy policy|Modern Slavery Act Transparency Statement|Sitemap|About US| Contact US: help@patsnap.com