Copper strip rolling production process flow
A production process, copper strip technology, applied in metal rolling, manufacturing tools, metal rolling, etc., can solve problems such as affecting production efficiency, inability to correct, difficult to control plate shape, etc., to facilitate process production and circulation, save money Labor and cost, the effect of improving production efficiency
- Summary
- Abstract
- Description
- Claims
- Application Information
AI Technical Summary
Problems solved by technology
Method used
Image
Examples
Embodiment
[0030] A copper strip rolling production process, comprising the following steps:
[0031] 1) Melting: Put the raw materials into the melting furnace for heating and melting, set the temperature of the melting furnace to 1090°C, and process it into a copper ingot with a thickness of 210cm through a drawing casting machine;
[0032] 2) hot rolling: put the copper ingot into a hot rolling mill and roll it into a strip blank with a thickness of 17cm;
[0033] 3) Face milling: the strip embryo is milled by a milling machine to remove the strip embryo with a thickness of 16cm on the upper and lower surface layers;
[0034] 4) Rough rolling: Use a rolling mill to roll out the preliminary shape of the copper strip, the preset thickness is controlled at 2.0cm, and the spacing between the rolls is adjusted repeatedly until the copper strip that meets the thickness standard is rolled out;
[0035] 5) Annealing: Bell furnace annealing, the annealing temperature is about 460°C, heat pres...
PUM
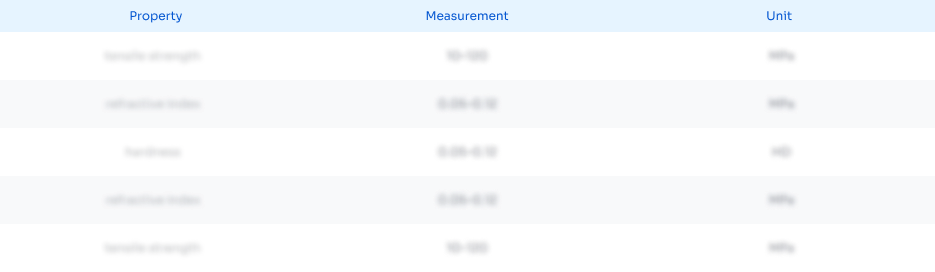
Abstract
Description
Claims
Application Information

- Generate Ideas
- Intellectual Property
- Life Sciences
- Materials
- Tech Scout
- Unparalleled Data Quality
- Higher Quality Content
- 60% Fewer Hallucinations
Browse by: Latest US Patents, China's latest patents, Technical Efficacy Thesaurus, Application Domain, Technology Topic, Popular Technical Reports.
© 2025 PatSnap. All rights reserved.Legal|Privacy policy|Modern Slavery Act Transparency Statement|Sitemap|About US| Contact US: help@patsnap.com