Microencapsulated curing agent, and water-based inorganic zinc-rich anticorrosive coating based on microencapsulated curing agent
A technology of microencapsulation and anti-corrosion coating, applied in anti-corrosion coatings, alkali metal silicate coatings, coatings, etc., can solve problems such as poor water resistance
- Summary
- Abstract
- Description
- Claims
- Application Information
AI Technical Summary
Problems solved by technology
Method used
Image
Examples
Embodiment 1
[0039] Present embodiment first prepares microencapsulated curing agent as follows:
[0040] Step 1. Add 5 g of sodium fluoroborate into 300 mL of absolute ethanol to prepare a curing agent slurry with a mass concentration of 2%.
[0041] Step 2. Raise the temperature of the curing agent slurry to 45°C, and then keep the temperature constant.
[0042] Step 3. Add 15 mL of deionized water and 0.2 g of CTAB to the curing agent slurry while stirring.
[0043] Step 4. Add 3mL of ammonia water with a mass concentration of 15% to the curing agent slurry while stirring, then slowly add 2g of tetraethyl orthosilicate (TEOS) dropwise. Ethyl ester is hydrolyzed and polycondensed under the catalysis of ammonia water; the reacted suspension is centrifuged, washed with absolute ethanol, and dried to obtain a microencapsulated curing agent, wherein the mass of the silica shell accounts for 11.5% of the mass of the curing agent.
[0044] Sodium fluoroborate (SFB) used in this embodiment an...
Embodiment 2
[0053] Present embodiment first prepares microencapsulated curing agent as follows:
[0054] Step 1. Add 10 g of sodium fluorosilicate into 400 mL of absolute ethanol to prepare a curing agent slurry with a mass concentration of 3%.
[0055] Step 2. Raise the temperature of the curing agent slurry to 50°C, and then keep the temperature constant.
[0056] Step 3. Add 10 mL of deionized water and 0.3 g of CTAB to the curing agent slurry while stirring.
[0057] Step 4. Add 2 mL of ammonia water with a mass concentration of 28% to the curing agent slurry while stirring, and then dropwise add 3 g of tetraethyl orthosilicate (TEOS). Hydrolysis and polycondensation under the catalysis of ammonia water; centrifuging the reacted suspension, washing with absolute ethanol, and drying to obtain a microencapsulated curing agent, wherein the mass of the silica shell accounts for 8.7% of the mass of the curing agent.
[0058] Sodium fluorosilicate (SFS) used in this embodiment and the mic...
Embodiment 3
[0067] In this embodiment, the microencapsulated curing agent and the water-based inorganic zinc-rich anticorrosion coating are prepared in the same manner as in Example 1, the difference is only that the amount of tetraethyl orthosilicate (TEOS) is changed to 0.1g, and the silica shell layer The mass accounts for 0.6% of the curing agent mass. After a period of mixing and stirring of the prepared coating, more agglomerated large particle solids will be produced, indicating that the amount of silica shell coating is less, resulting in faster release of the curing agent, and the coating will fail due to agglomeration.
PUM
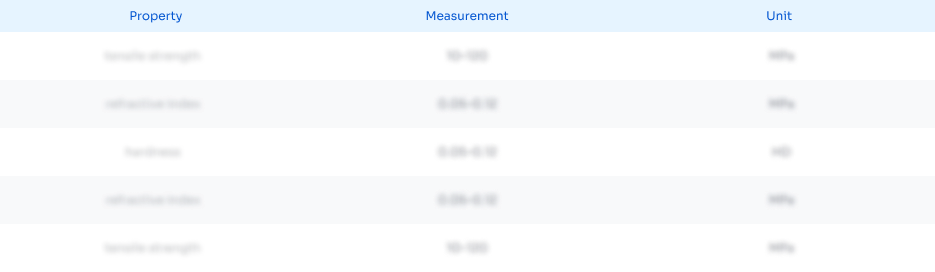
Abstract
Description
Claims
Application Information

- R&D
- Intellectual Property
- Life Sciences
- Materials
- Tech Scout
- Unparalleled Data Quality
- Higher Quality Content
- 60% Fewer Hallucinations
Browse by: Latest US Patents, China's latest patents, Technical Efficacy Thesaurus, Application Domain, Technology Topic, Popular Technical Reports.
© 2025 PatSnap. All rights reserved.Legal|Privacy policy|Modern Slavery Act Transparency Statement|Sitemap|About US| Contact US: help@patsnap.com