Automatic magnetic material production line structure
An automatic production line and magnetic material technology, applied in chemical instruments and methods, solid separation, separating solids from solids with airflow, etc., can solve the problems of delay in screening progress, blockage of sieve plate sieve holes, long time required, etc.
- Summary
- Abstract
- Description
- Claims
- Application Information
AI Technical Summary
Problems solved by technology
Method used
Image
Examples
Embodiment 1
[0025] refer to Figure 1-3 , a magnetic material automatic production line structure, comprising a screen box 1, the inner walls of both sides of the screen box 1 are fixedly connected with blowing plates 16, and the top outer walls of the two blowing plates 16 are provided with blowing holes 17 at equal distances, the two The four blowing plates 16 are arranged in eight rows, and the outer walls of the two sides of the screen box 1 near the two blowing plates 16 are fixedly connected with mounting plates 7, and the top outer walls of the two mounting plates 7 are fixedly connected with blowers 6, and the two The air blowing end of each air blower 16 is all fixedly connected with air delivery pipe 13, and the other end of air delivery pipe 13 is fixedly connected in the inside of blast plate 16, and the bottom inwall of screen box 1 is fixedly connected with tapered material distribution plate 19, and the screen box 1 There are feeding holes 8 on both sides of the outer walls...
Embodiment 2
[0034] refer to Figure 1-4, a magnetic material automatic production line structure, comprising a screen box 1, the inner walls of both sides of the screen box 1 are fixedly connected with blowing plates 16, and the top outer walls of the two blowing plates 16 are provided with blowing holes 17 at equal distances, the two The four blowing plates 16 are arranged in eight rows, and the outer walls of the two sides of the screen box 1 near the two blowing plates 16 are fixedly connected with mounting plates 7, and the top outer walls of the two mounting plates 7 are fixedly connected with blowers 6, and the two The air blowing end of each air blower 16 is all fixedly connected with air delivery pipe 13, and the other end of air delivery pipe 13 is fixedly connected in the inside of blast plate 16, and the bottom inwall of screen box 1 is fixedly connected with tapered material distribution plate 19, and the screen box 1 There are feeding holes 8 on both sides of the outer wall n...
PUM
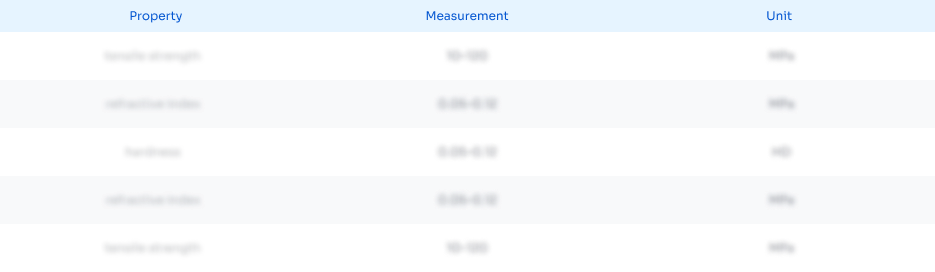
Abstract
Description
Claims
Application Information

- R&D
- Intellectual Property
- Life Sciences
- Materials
- Tech Scout
- Unparalleled Data Quality
- Higher Quality Content
- 60% Fewer Hallucinations
Browse by: Latest US Patents, China's latest patents, Technical Efficacy Thesaurus, Application Domain, Technology Topic, Popular Technical Reports.
© 2025 PatSnap. All rights reserved.Legal|Privacy policy|Modern Slavery Act Transparency Statement|Sitemap|About US| Contact US: help@patsnap.com