Characterization method for dynamic fracture performance of metal material
A technology of metal materials and fracture performance, which is applied in the direction of analyzing materials, using applied repetitive force/pulsation force to test material strength and strength characteristics, etc. It can solve the problems that the results are not necessarily accurate, the stress intensity factor is difficult to measure in real time, and the design and connection of test pieces are difficult and other issues to achieve the effect of avoiding interference
- Summary
- Abstract
- Description
- Claims
- Application Information
AI Technical Summary
Problems solved by technology
Method used
Image
Examples
Embodiment 1
[0048] A quasi-in-situ experimental analysis method for dynamic deformation and failure behavior of metal materials, the steps of which are as follows:
[0049] (1) Prepare standard three-point bending samples of aluminum alloy, the dimensions of which are: B is 3mm, W=2B, S=4W, L=13mm;
[0050] (2) The end of the incident rod and the front end of the transmission rod of the separated Hopkinson pressure rod with a diameter of 30 mm are equipped with punches for loading and supporting the sample. Strain gauges are attached to the incident rod and the transmission rod. For step (1 ) The prepared sample is dynamically loaded with a loading air pressure of 2 atm on a separate Hopkinson pressure rod equipped with a punch, so that the sample is destroyed during the first round of stress wave loading, and the loading process is obtained through the signal acquisition system Stress-time curves of incident wave, transmitted wave and reflected wave;
[0051] (3) Calculate the three str...
Embodiment 2
[0057] A quasi-in-situ experimental analysis method for dynamic deformation and failure behavior of metal materials, the steps of which are as follows:
[0058] (1) prepare a standard three-point bending sample of steel, its size is: B is 3mm, W=2B, S=4W, L=15mm;
[0059] (2) The end of the incident rod and the front end of the transmission rod of the separated Hopkinson pressure rod with a diameter of 35 mm are equipped with punches for loading and supporting the sample. Strain gauges are attached to the incident rod and the transmission rod. ) The prepared sample is dynamically loaded with a loading air pressure of 3atm on a separate Hopkinson pressure rod equipped with a punch, so that the sample is destroyed during the first round of stress wave loading, and the loading process is obtained through the signal acquisition system Stress-time curves of incident wave, transmitted wave and reflected wave;
[0060] (3) Calculate the stress-time curves of the incident wave, trans...
Embodiment 3
[0063] A quasi-in-situ experimental analysis method for dynamic deformation and failure behavior of metal materials, the steps of which are as follows:
[0064] (1) prepare a standard three-point bending sample of titanium alloy, its size is: B is 4mm, W=2B, S=4W, L=18mm;
[0065] (2) The end of the incident rod and the front end of the transmission rod of the separated Hopkinson pressure rod with a diameter of 40 mm are equipped with punches for loading and supporting the sample. Strain gauges are attached to the incident rod and the transmission rod. For step (1 ) The prepared sample is dynamically loaded with a loading air pressure of 3.5atm on a separate Hopkinson pressure rod equipped with a punch, so that the sample is destroyed in the first round of stress wave loading process, and the load is obtained through the signal acquisition system Stress-time curves of incident, transmitted and reflected waves in the process;
[0066] (3) Calculate the stress-time curves of th...
PUM
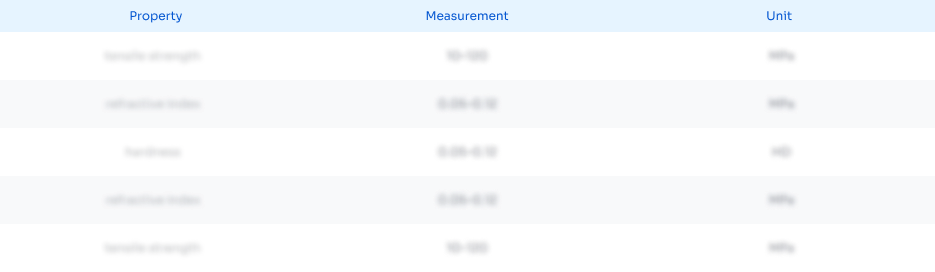
Abstract
Description
Claims
Application Information

- R&D
- Intellectual Property
- Life Sciences
- Materials
- Tech Scout
- Unparalleled Data Quality
- Higher Quality Content
- 60% Fewer Hallucinations
Browse by: Latest US Patents, China's latest patents, Technical Efficacy Thesaurus, Application Domain, Technology Topic, Popular Technical Reports.
© 2025 PatSnap. All rights reserved.Legal|Privacy policy|Modern Slavery Act Transparency Statement|Sitemap|About US| Contact US: help@patsnap.com