Method for reducing auxiliary material consumption of electric furnace oxidation method
A technology of auxiliary materials and electric furnace, which is applied in the field of electric furnace oxidation steelmaking to reduce the consumption of auxiliary materials in electric furnace oxidation, can solve the problems of excessive consumption of auxiliary materials, achieve the effects of expanding the flow range, improving utilization rate, and increasing the reaction speed of slag and gold
- Summary
- Abstract
- Description
- Claims
- Application Information
AI Technical Summary
Problems solved by technology
Method used
Image
Examples
Embodiment
[0033] This embodiment provides two groups of techniques for smelting steel using the method of the present invention, such as examples 1 and 2; simultaneously, a group of techniques for using the traditional electric furnace oxidation method for bottomless blowing of the same kind of steel is provided, such as comparative example 3, and the specific smelting process includes Follow the steps below:
[0034] 1. Leave a furnace for smelting steel in the electric furnace, then add auxiliary materials and scrap steel materials into the furnace, and melt the materials after electrifying the furnace, and add carbon powder during the melting process of the materials, and blow oxygen into the furnace at the same time, the specific process parameters As shown in Table 1.
[0035] Table 1 EAF steelmaking process parameters
[0036]
[0037] 2. Examples 1 and 2, the bottom blowing gas mode is used in the smelting process, and N is used when the blowing starts to 1 / 3 stage 2 , the c...
PUM
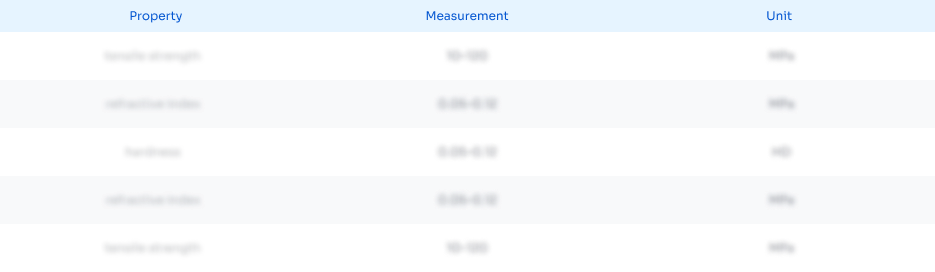
Abstract
Description
Claims
Application Information

- R&D
- Intellectual Property
- Life Sciences
- Materials
- Tech Scout
- Unparalleled Data Quality
- Higher Quality Content
- 60% Fewer Hallucinations
Browse by: Latest US Patents, China's latest patents, Technical Efficacy Thesaurus, Application Domain, Technology Topic, Popular Technical Reports.
© 2025 PatSnap. All rights reserved.Legal|Privacy policy|Modern Slavery Act Transparency Statement|Sitemap|About US| Contact US: help@patsnap.com