Device and method for smelting metal through thermal reduction method
A technology of reduction method and heating device, which is applied in the field of metal smelting, can solve the problems of poor kinetic conditions and large energy consumption, and achieve the effects of improving efficiency, increasing contact area, and improving kinetic conditions
- Summary
- Abstract
- Description
- Claims
- Application Information
AI Technical Summary
Problems solved by technology
Method used
Image
Examples
Embodiment 1
[0032] A device for smelting metals by thermal reduction, such as figure 1 As shown, it specifically includes a smelting furnace 1, a heating device 2, an ore powder injection device 3, a reducing agent injection device 4, a slagging agent injection device 5, a metal discharge device 6 and a tail gas export device 7, wherein the heating device 2, Mineral powder injection device 3 and reducing agent injection device 4 are arranged at the upper part of smelting furnace 1;
[0033] In addition, more than one ore powder injection device 3, reducing agent injection device 4 and slagging agent injection device 5 are arranged in the circumferential direction of smelting furnace 1, and the nozzles thereof can be inclined upward or downward; The blowing device can be arranged on one level or multiple levels of the smelting furnace 1; in the height direction of the smelting furnace 1, the reducing agent injection device 4 can be lower than the ore powder injection device 3, or higher th...
Embodiment 2
[0036] A kind of method adopting the device in embodiment 1 to carry out thermal reduction method smelting metal, concrete steps are as follows:
[0037] (1) In the upper part of the smelting furnace 1, the ore powder in the ore powder tank is blown into the smelting furnace 1 by the ore powder injection device 3, and the reducing agent blown in by the reducing agent injection device 4 is under the heating state of the heating device 2 Reaction, enter the lower part of the smelting furnace 1 after the reaction is completed;
[0038] (2) The metal formed by the reaction in step (1) is removed from the metal discharge device 6, and the impurities formed form slag under the action of the slagging agent blown into by the slagging agent injection device 5;
[0039] (3) The reducing tail gas formed by the reaction in step (1) is discharged through the tail gas exporting device 7 .
[0040] Wherein the reduction tail gas is discharged through the tail gas exporting device 7 and ente...
Embodiment 3
[0042] A kind of smelting method that adopts the device in embodiment 1 to carry out metallic iron, its technological process is as follows figure 2 As shown, the specific steps are as follows:
[0043] First of all, the smelting furnace is built with refractory bricks, which are divided into upper and lower parts by a partition. There are holes in the partition, and there is a high-temperature spray coating on the partition. The upper part belongs to the reduction area (with iron ore powder injection device, reducing agent Injection device, furnace top with heating device arc), reducing gas H 2 Injection port, the arc heating on the top of the furnace injects iron ore powder and H into the upper part 2 , maintaining a temperature of 1300°C for redox reactions, making H 2 It can quickly and fully reduce iron ore powder, and the reduced iron-containing materials flow into the lower part through the upper and lower partition holes of the smelting furnace.
[0044]Secondly, t...
PUM
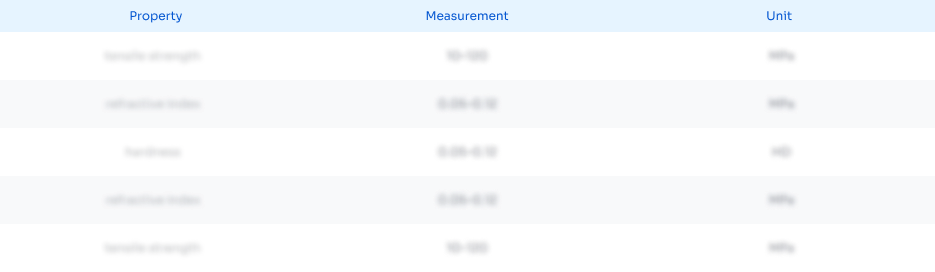
Abstract
Description
Claims
Application Information

- R&D
- Intellectual Property
- Life Sciences
- Materials
- Tech Scout
- Unparalleled Data Quality
- Higher Quality Content
- 60% Fewer Hallucinations
Browse by: Latest US Patents, China's latest patents, Technical Efficacy Thesaurus, Application Domain, Technology Topic, Popular Technical Reports.
© 2025 PatSnap. All rights reserved.Legal|Privacy policy|Modern Slavery Act Transparency Statement|Sitemap|About US| Contact US: help@patsnap.com