Bidirectional shearing type inertial damper
A two-way shearing and damper technology, applied in building types, building components, shock-proof and other directions, can solve the problems of collision between shearing frame and shell, weakening damping effect, poor suppression effect, etc., to achieve negative stiffness effect, lifting and reducing Vibration effect, the effect of eliminating the weakening effect
- Summary
- Abstract
- Description
- Claims
- Application Information
AI Technical Summary
Problems solved by technology
Method used
Image
Examples
Embodiment Construction
[0027] The present invention will be described in detail below in conjunction with the accompanying drawings and specific embodiments.
[0028] see Figure 1~4 , For example, a two-way shear type inertial damper includes: a housing 4, which is filled with a viscous medium; two rotating structures are relatively and spaced on the housing 4, and the rotating structures include a gear 10, an inertial disc 11 and the rotating shaft 9, the rotating shaft 9 is rotatably arranged in the housing 4, one end of the rotating shaft 9 extends out of the housing 4 and is connected with the inertia disk 11, the gear 10 is sleeved on the rotating shaft 9, the gear 10 is fixed relative to the rotating shaft 9; the protective cover 3 and the shear frame 7, the protective cover 3 is set on the shell 4 and is used to connect the vibration structure, and the shear frame 7 is fixedly arranged on the In the protective cover 3 and meshed with the two gears 10, when the vibrating structure vibrates a...
PUM
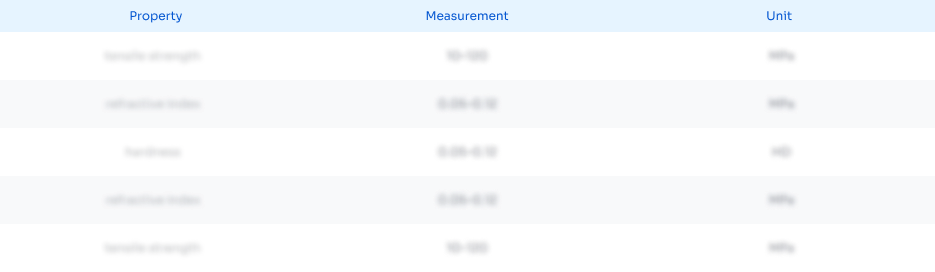
Abstract
Description
Claims
Application Information

- R&D
- Intellectual Property
- Life Sciences
- Materials
- Tech Scout
- Unparalleled Data Quality
- Higher Quality Content
- 60% Fewer Hallucinations
Browse by: Latest US Patents, China's latest patents, Technical Efficacy Thesaurus, Application Domain, Technology Topic, Popular Technical Reports.
© 2025 PatSnap. All rights reserved.Legal|Privacy policy|Modern Slavery Act Transparency Statement|Sitemap|About US| Contact US: help@patsnap.com