Multi-chamber magnetic control multilayer optical coating equipment and method
An optical coating and magnetron technology, applied in coating, sputtering coating, ion implantation coating, etc., can solve the problems that the uniformity of the working gas is difficult to control, affects the coating quality of the workpiece, and the quality of the coating layer of the workpiece is different. , to achieve the effect of improving vacuum uniformity, high consistency, and improving coating quality
- Summary
- Abstract
- Description
- Claims
- Application Information
AI Technical Summary
Problems solved by technology
Method used
Image
Examples
Embodiment 1
[0046] This embodiment is a multi-chamber magnetron multi-layer optical coating equipment, such as figure 1 As shown, it includes a workpiece loading platform 1, a workpiece unloading platform 2, a workpiece in and out device 3, a pretreatment chamber 4, a workpiece in and out conversion chamber 5, and three coating chambers 6. The pretreatment chamber and the three coating chambers are distributed in the workpiece in and out. Around the conversion chamber, the workpiece loading platform and the workpiece unloading platform are distributed on the two outer sides of the workpiece in and out of the device in different directions. A first vacuum door valve mechanism 7 is provided at the connection between the workpiece in and out of the conversion chamber and the pretreatment chamber, and a second vacuum door valve mechanism 8 is provided at the connection between the workpiece in and out of the conversion chamber and each coating chamber, and the pretreatment chamber faces the wo...
Embodiment 2
[0057] The present embodiment is a multi-chamber magnetron multilayer optical coating method, which is realized by the coating equipment described in Embodiment 1, and includes the following steps:
[0058] (1) The workpiece rack carries each workpiece, and is sent into the pretreatment chamber by the workpiece entry and exit device for ion surface treatment;
[0059] (2) after finishing the ion surface treatment, open the first vacuum gate valve mechanism, wait for the workpiece rack of the workpiece coating to enter the workpiece entry and exit conversion chamber, and then close the first vacuum gate valve mechanism;
[0060] (3) The workpiece rack waiting for the workpiece to be coated is lifted to the upper part of the workpiece in and out of the conversion chamber;
[0061] (4) After the coating of one of the coating chambers is completed, first open the second vacuum gate valve mechanism and send out the workpiece rack that has completed the workpiece coating, then close...
PUM
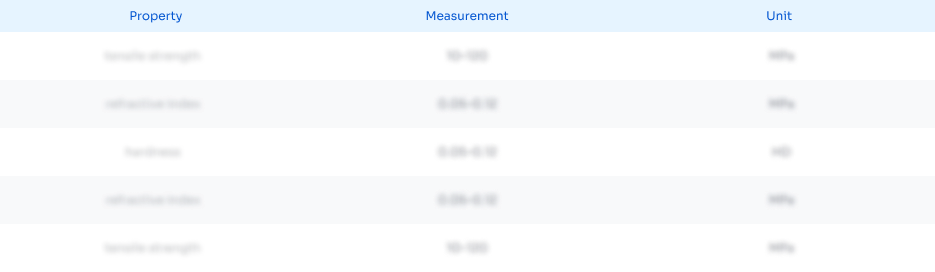
Abstract
Description
Claims
Application Information

- Generate Ideas
- Intellectual Property
- Life Sciences
- Materials
- Tech Scout
- Unparalleled Data Quality
- Higher Quality Content
- 60% Fewer Hallucinations
Browse by: Latest US Patents, China's latest patents, Technical Efficacy Thesaurus, Application Domain, Technology Topic, Popular Technical Reports.
© 2025 PatSnap. All rights reserved.Legal|Privacy policy|Modern Slavery Act Transparency Statement|Sitemap|About US| Contact US: help@patsnap.com