Stress relief annealing process of non-quenched and tempered steel for direct cutting
A technology of stress relief annealing and non-quenched and tempered steel, applied in the field of steel heat treatment, can solve the problem of high surface hardness, achieve the effects of low equipment requirements, prevent cracking, and shorten the production cycle
- Summary
- Abstract
- Description
- Claims
- Application Information
AI Technical Summary
Problems solved by technology
Method used
Image
Examples
Embodiment 1
[0023] (1) Put the size of the non-tangible steel after the specification φ85, the straight cut, in the middle, and the tail is bundled, the purpose is to prevent straightening of the round steel bending rebound; then put in the specification is 9.8m * 3.5m * 3M trolley type annealing furnace, where annealing furnace under the upper housing is ≥ 500mm, the spacer spacer is separated from the rail, the spacing is 1200mm, ensuring the burner flame operation within the horn gap; the side wall of the annealing furnace Distributed 16 thermocouples accurately measure the temperature of the furnace;
[0024] (2) The annealing furnace is warmed to 450 ° C, and the temperature is 70 ° C / h.
[0025] (3) The holding time is stopped and heated, and the non-regulatory steel is cooled to 300 ° C with the furnace, and the cooling rate is 30 ° C / h.
[0026] (4) After cooling, directly cut the non-tangible steel remove the annealing furnace, air cooling to room temperature.
Embodiment 2
[0028] (1) Put the specification φ110, straight cut into the head of non-tangible steel, in the middle, and the tail is bundled, the purpose is to prevent straightening of round steel bending rebound; then put in the specification is 9.8m * 3.5m * 3M trolley type annealing furnace, where annealing furnace under the upper housing is ≥ 500mm, the spacer spacer is separated from the rail, the spacing is 1200mm, ensuring the burner flame operation within the horn gap; the side wall of the annealing furnace Distributed 16 thermocouples accurately measure the temperature of the furnace;
[0029] (2) The annealing furnace is warmed to 520 ° C, and the temperature is 70 ° C / hr, heat insulation for 18 hours;
[0030] (3) After the holding time is stopped, the heating is stopped, and the non-regulatable steel is cut directly to 150 ° C, and the cooling rate is 50 ° C / h.
[0031] (4) After cooling, directly cut the non-tangible steel remove the annealing furnace, air cooling to room temp...
Embodiment 3
[0033] (1) Put the size of the non-tangible steel after the specification φ140, the straight cut, in the middle, and the tail is bundled, the purpose is to prevent straightening of the round steel bending rebound; then put in the specification 9.8m * 3.5m * 3M trolley type annealing furnace, where annealing furnace under the upper housing is ≥ 500mm, the spacer spacer is separated from the rail, the spacing is 1200mm, ensuring the burner flame operation within the horn gap; the side wall of the annealing furnace Distributed 16 thermocouples accurately measure the temperature of the furnace;
[0034] (2) The annealing furnace is warmed to 540 ° C, and the temperature increase rate is 70 ° C / h.
[0035] (3) The holding time is stopped and heated, and the non-regulatory steel is directly cut into 300 ° C, and the temperature is 40 ° C / h.
[0036] (4) After cooling, directly cut the non-tangible steel remove the annealing furnace, air cooling to room temperature.
PUM
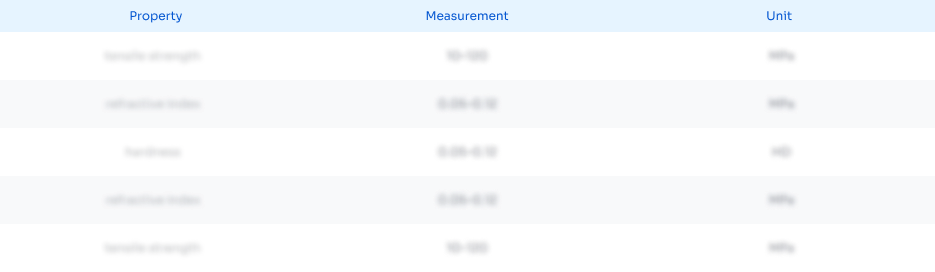
Abstract
Description
Claims
Application Information

- R&D
- Intellectual Property
- Life Sciences
- Materials
- Tech Scout
- Unparalleled Data Quality
- Higher Quality Content
- 60% Fewer Hallucinations
Browse by: Latest US Patents, China's latest patents, Technical Efficacy Thesaurus, Application Domain, Technology Topic, Popular Technical Reports.
© 2025 PatSnap. All rights reserved.Legal|Privacy policy|Modern Slavery Act Transparency Statement|Sitemap|About US| Contact US: help@patsnap.com