Method for preparing nano cobalt tungstate and recovering crude titanium slag
A technology of nano-tungsten and coarse titanium, applied in chemical instruments and methods, nanotechnology, chemical recycling, etc., can solve the problems of low recovery rate of titanium elements, economic benefits, low-cost investment, and low value of recycled products, so as to achieve value enhancement, Improved economy and high recovery rate
- Summary
- Abstract
- Description
- Claims
- Application Information
AI Technical Summary
Problems solved by technology
Method used
Examples
Embodiment 1
[0033] Example 1: A V 2 o 5 -WO 3 / TiO 2 A method for preparing nano-cobalt tungstate and reclaiming coarse titanium slag using waste SCR denitrification catalyst as raw material. The specific steps include:
[0034] (1) Pretreatment of waste catalyst
[0035] The waste catalyst was roasted at 550°C for 6 hours, and after soot blowing treatment, it was pulverized to below 300 mesh to obtain waste catalyst powder;
[0036] (2) Element separation
[0037] Uniformly mix the waste catalyst powder obtained after pretreatment with twice the mass of sodium chloride, and roast at 750°C for 6 hours; crush the sintered block obtained after roasting to 150 mesh, and use an ammonia solution with a volume concentration of 5% at a liquid-solid ratio 5:1 repeated leaching for 3 times, and then filtered to obtain sodium tungstate solution and titanium salt precipitation;
[0038] (3) Titanium recovery
[0039] Washing and drying the precipitate obtained in step (2) to obtain coarse tit...
Embodiment 2
[0045] Example 2: A V 2 o 5 -WO 3 / TiO 2 A method for preparing nano-cobalt tungstate and reclaiming coarse titanium slag using waste SCR denitrification catalyst as raw material. The specific steps include:
[0046] (1) Pretreatment of waste catalyst
[0047] The waste catalyst was calcined at 650°C for 4 hours, and after soot blowing treatment, it was pulverized to below 300 mesh to obtain waste catalyst powder;
[0048] (2) Element separation
[0049] Uniformly mix the waste catalyst powder obtained after pretreatment with 2.5 times the mass of sodium chloride, and roast at 800°C for 5 hours; crush the obtained agglomerate to 150 meshes, and use an ammonia solution with a volume concentration of 7% at a liquid-solid ratio 6:1 repeated leaching twice, and then filtered to obtain sodium tungstate solution and titanium salt precipitation;
[0050] (3) Titanium recovery
[0051] Washing and drying the precipitate obtained in step (2) to obtain coarse titanium slag, and c...
Embodiment 3
[0057] Example 3: A V 2 o 5 -WO 3 / TiO 2 A method for preparing nano-cobalt tungstate and reclaiming coarse titanium slag using waste SCR denitrification catalyst as raw material. The specific steps include:
[0058] (1) Pretreatment of waste catalyst
[0059] The waste catalyst was roasted at 750°C for 3 hours, and after soot blowing treatment, it was pulverized to below 300 mesh to obtain waste catalyst powder;
[0060] (2) Element separation
[0061] Uniformly mix the waste catalyst powder obtained after pretreatment with 3 times the mass of sodium chloride, and roast at 850°C for 3 hours; crush the sintered block obtained after roasting to 150 mesh, and use an ammonia solution with a volume concentration of 10% at a liquid-solid ratio 10:1 repeated leaching once, and then filtered to obtain sodium tungstate solution and titanium salt precipitation;
[0062] (3) Titanium recovery
[0063] Washing and drying the precipitate obtained in step (2) to obtain coarse titani...
PUM
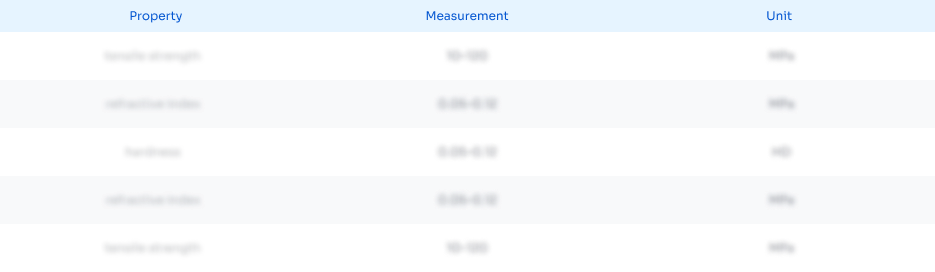
Abstract
Description
Claims
Application Information

- R&D Engineer
- R&D Manager
- IP Professional
- Industry Leading Data Capabilities
- Powerful AI technology
- Patent DNA Extraction
Browse by: Latest US Patents, China's latest patents, Technical Efficacy Thesaurus, Application Domain, Technology Topic, Popular Technical Reports.
© 2024 PatSnap. All rights reserved.Legal|Privacy policy|Modern Slavery Act Transparency Statement|Sitemap|About US| Contact US: help@patsnap.com