Device for polishing welding seam inside pressure vessel
A pressure vessel, internal welding technology, applied in grinding/polishing safety devices, grinding machines, grinding racks, etc., can solve the problems of environmental protection, low grinding efficiency and unsafety
- Summary
- Abstract
- Description
- Claims
- Application Information
AI Technical Summary
Problems solved by technology
Method used
Image
Examples
Embodiment 1
[0066] The embodiment of the present invention discloses a pressure vessel internal weld seam grinding device 8, such as figure 1 shown, including:
[0067] A moving seat 1, a plurality of moving wheels 11 are arranged at the lower end of the moving seat 1;
[0068] The first angle adjustment device 2 is installed on the upper end of the moving seat 1;
[0069] Mounting seat 3, the lower end is installed on the working end of the upper end of the first angle adjustment device 2, the upper end of the mounting seat 3 is installed with the pressure vessel 4 to be polished, and at least one end of the pressure vessel 4 to be polished is provided with a detachable head 41. The mounting base 3 or the moving base 1 is also connected with a dust collection device 5;
[0070] The fixed seat 6 is located on one side of the mobile seat 1, and the side of the mobile seat 1 close to the fixed seat 6 is provided with a limit block 61, and the limit block 61 is used to be inserted into the...
Embodiment 2
[0089] On the basis of Example 1, such as figure 1 As shown, the first angle adjusting device 2 includes: several third telescopic rods 21, which are evenly arranged along the peripheral side of the mounting seat 3, and the lower ends of the third telescopic rods 21 are fixedly connected to the upper end of the moving seat 1, The upper end of the third telescopic rod 21 is rotatably connected to the lower end of the mounting base 3 through a hinge seat 22 . (Preferably, the hinge seat on the left side can also be fixed to the mounting seat, and the hinge seat on the right side can be slidably connected to the mounting seat)
[0090] The beneficial effect of the above technical solution is that: the above first angle adjusting device has the advantage of simple structure.
Embodiment 3
[0092] On the basis of embodiment 1 or 2, such as image 3 As shown, the dust outlet of the dust suction device 5 is also connected with a dust collection box 10, and the mounting base 3 or the moving base 1 is also connected with a mounting mechanism 9, and the mounting mechanism 9 includes:
[0093] An installation box 91, the upper end of the installation box 91 is provided with a first installation through hole 92, and the lower end of the dust collection box 10 is provided with a first positioning block 101 for inserting into the first installation through hole 92;
[0094] The fixed block 93 is fixedly connected to the upper end of the installation box 91 and is located on one side of the dust collection box 10. The upper part of the fixed block 93 is provided with a second installation through hole 919;
[0095] The second positioning block 102 is arranged on the side wall of the dust box 10, and the second positioning block 102 is used to be inserted into the second in...
PUM
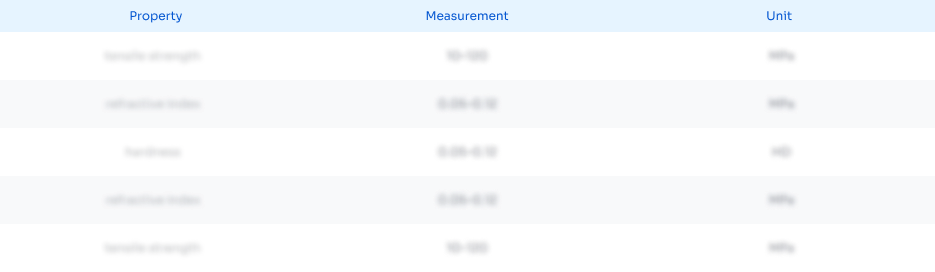
Abstract
Description
Claims
Application Information

- Generate Ideas
- Intellectual Property
- Life Sciences
- Materials
- Tech Scout
- Unparalleled Data Quality
- Higher Quality Content
- 60% Fewer Hallucinations
Browse by: Latest US Patents, China's latest patents, Technical Efficacy Thesaurus, Application Domain, Technology Topic, Popular Technical Reports.
© 2025 PatSnap. All rights reserved.Legal|Privacy policy|Modern Slavery Act Transparency Statement|Sitemap|About US| Contact US: help@patsnap.com