Permanent magnet synchronous motor robust control system and method
A permanent magnet synchronous motor, robust control technology, applied in the control system, vector control system, motor generator control and other directions, can solve the problems of poor dynamic performance and robustness of the control system, large amount of calculation, etc., to achieve strong anti-disturbance Capability and robustness, low computational cost, damage avoidance effect
- Summary
- Abstract
- Description
- Claims
- Application Information
AI Technical Summary
Problems solved by technology
Method used
Image
Examples
Embodiment Construction
[0038] In order to illustrate the technical solutions of the present invention, the present invention will be further described below in conjunction with the accompanying drawings.
[0039] The present invention provides a permanent magnet synchronous motor robust control system, such as figure 1 As shown, including speed / position sensor module, current sensor module, Clark transformation module, Park transformation module, speed-current prediction controller module, current limiter module, inverse Park transformation module, SVPWM module, permanent magnet synchronous motor PMSM module and inverter module.
[0040] The speed / position sensor module is respectively connected with the permanent magnet synchronous motor PMSM module, Park transformation module, inverse Park transformation module and speed-current prediction controller module, and is used to collect the position angle θ and mechanical angular velocity ω of the permanent magnet synchronous motor PMSM module m , inpu...
PUM
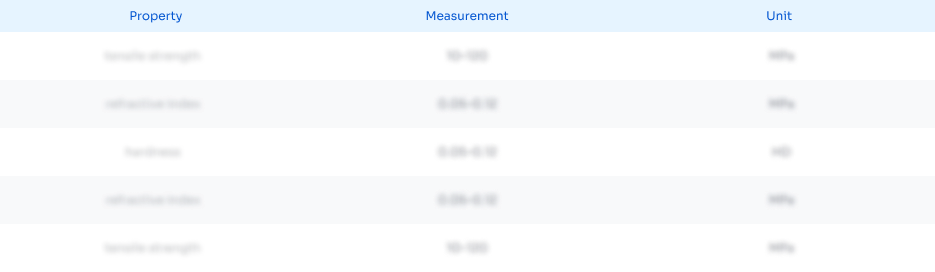
Abstract
Description
Claims
Application Information

- Generate Ideas
- Intellectual Property
- Life Sciences
- Materials
- Tech Scout
- Unparalleled Data Quality
- Higher Quality Content
- 60% Fewer Hallucinations
Browse by: Latest US Patents, China's latest patents, Technical Efficacy Thesaurus, Application Domain, Technology Topic, Popular Technical Reports.
© 2025 PatSnap. All rights reserved.Legal|Privacy policy|Modern Slavery Act Transparency Statement|Sitemap|About US| Contact US: help@patsnap.com