Comprehensive recovery and beneficiation process for wolframite and scheelite and associated valuable metals of wolframite and scheelite
A technology of valuable metals, black and white tungsten, applied in the field of beneficiation technology, can solve the problems of low recovery rate of tungsten ore and large dosage of chemicals, and achieve the effects of improving comprehensive utilization rate, low production cost and simple process flow
- Summary
- Abstract
- Description
- Claims
- Application Information
AI Technical Summary
Problems solved by technology
Method used
Image
Examples
Embodiment 1
[0042] An ore body in Jiangxi, the ore contains 0.119% tungsten, 0.1% molybdenum, and 0.2% copper, and the raw ore dosage is 300g.
[0043] The beneficiation process includes the following steps:
[0044] (1) After the ore is crushed, the ore is ground to a fineness of -0.075mm, accounting for 55%, and then a copper-molybdenum mixed coarse concentrate and copper-molybdenum flotation tailings are obtained through a rough separation; wherein, the concentration of the flotation pulp is 30%; The molybdenum collector is butyl xanthate and thiocarbamate, the dosage is 85g / t and 15g / t respectively; the foaming agent is methyl isobutyl carbinol, the dosage is 25g / t; the gangue inhibitor is water glass , the dosage is 1200g / t;
[0045] (2) Grind the above-mentioned copper-molybdenum mixed coarse concentrate until the fineness is -0.038mm, which accounts for 77%, and then use floating molybdenum to suppress copper to separate. Copper concentrate was obtained; among them, the concentra...
Embodiment 2
[0051] In an ore body in Inner Mongolia, the ore contains 0.13% tungsten, 0.09% molybdenum, and 0.30% copper, and the raw ore consumption is 300g.
[0052] The beneficiation process includes the following steps:
[0053] (1) After the ore is crushed, the ore is ground to a fineness of -0.075mm, accounting for 60%, and then a copper-molybdenum mixed coarse concentrate and copper-molybdenum flotation tailings are obtained through a rough separation; wherein, the concentration of the flotation pulp is 30%; The molybdenum collector is butyl xanthate and thiocarbamate, the dosage is 80g / t and 20g / t respectively; the foaming agent is methyl isobutyl carbinol, the dosage is 30g / t; the gangue inhibitor is water glass , the dosage is 1000g / t;
[0054] (2) Grind the above-mentioned copper-molybdenum mixed coarse concentrate until the fineness is -0.038mm, accounting for 80%, and then use floating molybdenum to suppress copper to separate, after a rough separation, four times of concent...
Embodiment 3
[0060] In a certain ore body in Liaoning, the ore contains 0.113% tungsten, 0.082% molybdenum, and 0.35% copper, and the raw ore consumption is 300g.
[0061] The beneficiation process includes the following steps:
[0062] (1) After the ore is crushed, it is ground to a fineness of -0.075mm, accounting for 50%, and then through a rough separation to obtain copper-molybdenum mixed coarse concentrate and copper-molybdenum flotation tailings; wherein, the concentration of flotation pulp is 35%; The molybdenum collector is butyl xanthate and thiocarbamate, the dosage is 90g / t and 10g / t respectively; the foaming agent is methyl isobutyl carbinol, the dosage is 20g / t; the gangue inhibitor is water glass , the dosage is 1300g / t;
[0063] (2) Grind the above-mentioned copper-molybdenum mixed coarse concentrate until the fineness is -0.038mm, accounting for 75%, and then use floating molybdenum to suppress copper to separate, after a rough separation, four times of concentration to o...
PUM
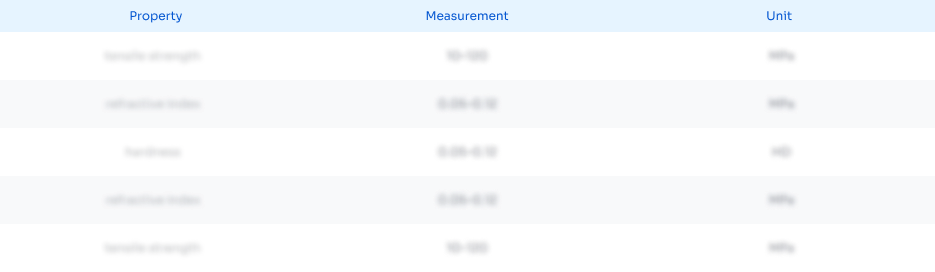
Abstract
Description
Claims
Application Information

- R&D Engineer
- R&D Manager
- IP Professional
- Industry Leading Data Capabilities
- Powerful AI technology
- Patent DNA Extraction
Browse by: Latest US Patents, China's latest patents, Technical Efficacy Thesaurus, Application Domain, Technology Topic, Popular Technical Reports.
© 2024 PatSnap. All rights reserved.Legal|Privacy policy|Modern Slavery Act Transparency Statement|Sitemap|About US| Contact US: help@patsnap.com