Electromagnetic rotary vibration energy collector
A vibration energy harvesting, electromagnetic technology, applied in the direction of generator/motor, piezoelectric effect/electrostrictive or magnetostrictive motor, electrical components, etc., can solve the problem of increasing the resonance frequency of the structure, small displacement, and failure of the acquisition structure And other issues
- Summary
- Abstract
- Description
- Claims
- Application Information
AI Technical Summary
Problems solved by technology
Method used
Image
Examples
specific Embodiment approach
[0053] The coil device includes: a polyethylene insulating frame 1, and the outer side of the insulating frame 1 is a fan ring structure arranged in a 90° circular array, with a central angle of 60°, an outer diameter of 23.5mm, an inner diameter of 19mm, and a height of 6mm; in order to increase The number of turns of the coil winding 2, the insulating frame 1 arranges a rectangular support 100 up and down, the upper rectangular support 100 has a height of 2.5 mm, a width of 2.5 mm, and a thickness of 1.5 mm, and the lower rectangular support 100 has a height of 7 mm and a width of 2.5 mm. The thickness is 1.5 mm. In order to increase the stability of the lower rectangular support 100, an equilateral right-angled triangle structure with a side length of 2 mm and a thickness of 1.5 mm is arranged between the left and right sides of the lower rectangular support 100 and the insulating frame 1, wherein two Two adjacent lower side brackets are fixed with input pins 141; the inner ...
PUM
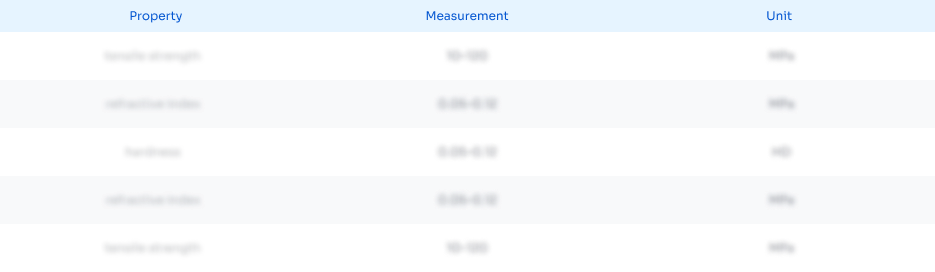
Abstract
Description
Claims
Application Information

- Generate Ideas
- Intellectual Property
- Life Sciences
- Materials
- Tech Scout
- Unparalleled Data Quality
- Higher Quality Content
- 60% Fewer Hallucinations
Browse by: Latest US Patents, China's latest patents, Technical Efficacy Thesaurus, Application Domain, Technology Topic, Popular Technical Reports.
© 2025 PatSnap. All rights reserved.Legal|Privacy policy|Modern Slavery Act Transparency Statement|Sitemap|About US| Contact US: help@patsnap.com