A clean production process for recovering molybdenum-rhenium from ion adsorption type molybdenum-rhenium ore
An ion-adsorption type, clean production technology, applied in the direction of improving process efficiency, etc., can solve the problems of unsuitable treatment of ion-adsorption molybdenum-rhenium ore, high safety requirements, and lack of treatment methods, so as to save long-distance transportation The effect of cost, environmental friendliness, and process is simple and easy to control
- Summary
- Abstract
- Description
- Claims
- Application Information
AI Technical Summary
Problems solved by technology
Method used
Image
Examples
Embodiment 1
[0036] A process for recovering molybdenum-rhenium from ion adsorption type molybdenum-rhenium ore, comprising the following steps:
[0037] (1) after ion adsorption type molybdenum-rhenium ore is ground to particle size less than 0.12mm in vibration mill, get 2kg and join in the reactor;
[0038](2) add 10L of tap water to the reactor with 3 baffles, add 1.5kg of sodium hydroxide simultaneously, be heated to 60 DEG C and carry out leaching for the first time, the leaching time is 2h, and the rotational speed of the axial flow paddle is 80rpm, After the reaction, vacuum filtration was used to separate solid-liquid, and the concentration of rhenium in the obtained primary leaching solution was 2.09 mg / L, and the concentration of molybdenum was 92.91 mg / L.
[0039] (3) the ion adsorption type molybdenum-rhenium ore processed in step (2) is continued to be added into the reactor, and 6L tap water, 900g sodium hydroxide, 80g hydrogen peroxide, 240g ammonium sulfate are added simul...
Embodiment 2
[0041] A process for recovering molybdenum-rhenium from ion adsorption type molybdenum-rhenium ore, comprising the following steps:
[0042] (1) after ion adsorption type molybdenum-rhenium ore is ground to particle size less than 0.12mm in vibration mill, get 2kg and join in the reactor;
[0043] (2) in the reactor with 3 baffle plates, add 10L tap water, add the potassium hydroxide of 1.5kg simultaneously, be heated to 60 ℃ and carry out leaching for the first time, the leaching time is 2h, and the rotational speed of the axial flow paddle is 80rpm, After the reaction, the solid-liquid separation was carried out by vacuum filtration, and the rhenium concentration in the obtained primary leaching solution was 2.06 mg / L, and the molybdenum concentration was 86.34 mg / L;
[0044] (3) the ion adsorption type molybdenum-rhenium ore processed in step (2) continues to be added to the reactor, and 6L tap water, 900g potassium hydroxide, 240g potassium permanganate, 100g sodium chlori...
Embodiment 3
[0046] A process for recovering molybdenum-rhenium from ion adsorption type molybdenum-rhenium ore, comprising the following steps:
[0047] (1) after ion adsorption type molybdenum-rhenium ore is ground to particle size less than 0.12mm in vibration mill, get 2kg and join in the reactor;
[0048] (2) add 10L of tap water to the reactor with 3 baffles, add 1.5kg of sodium hydroxide simultaneously, be heated to 60 DEG C and carry out leaching for the first time, the leaching time is 2h, and the rotational speed of the axial flow paddle is 80rpm, After the reaction, vacuum filtration was performed to separate solid-liquid, and the concentration of rhenium in the obtained primary leaching solution was 2.18 mg / L, and the concentration of molybdenum was 97.41 mg / L.
[0049] (3) the ion adsorption type molybdenum-rhenium ore processed in step (2) is continued to be added to the reactor, and 6L tap water, 900g of sodium hydroxide, 100g of hydrogen peroxide, 360g of ammonium sulfate a...
PUM
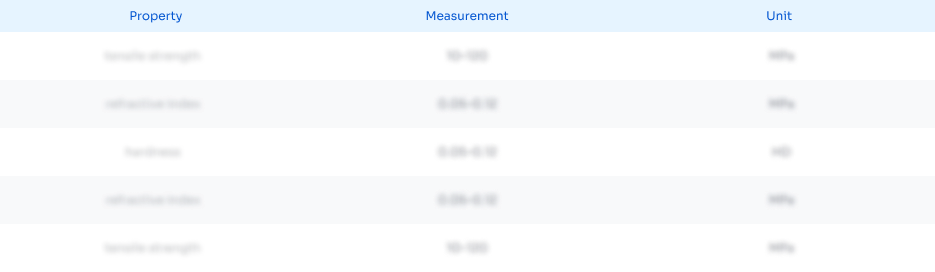
Abstract
Description
Claims
Application Information

- R&D
- Intellectual Property
- Life Sciences
- Materials
- Tech Scout
- Unparalleled Data Quality
- Higher Quality Content
- 60% Fewer Hallucinations
Browse by: Latest US Patents, China's latest patents, Technical Efficacy Thesaurus, Application Domain, Technology Topic, Popular Technical Reports.
© 2025 PatSnap. All rights reserved.Legal|Privacy policy|Modern Slavery Act Transparency Statement|Sitemap|About US| Contact US: help@patsnap.com