Method for cyclic regeneration of magnesium alkylation reaction catalyst
A technology of catalyst circulation and chemical reaction, applied in the direction of catalyst regeneration/reactivation, physical/chemical process catalysts, chemical instruments and methods, etc., can solve problems such as waste of resources, achieve no secondary pollution, high environmental and economic value, Avoid the effects of processing
- Summary
- Abstract
- Description
- Claims
- Application Information
AI Technical Summary
Problems solved by technology
Method used
Image
Examples
Embodiment 1
[0027] Such as figure 1 As shown, take 40 grams of spent magnesium oxide catalyst, after drying at 80 degrees Celsius, put it into a ball mill and pulverize it to more than 80 mesh. Put the pulverized spent magnesium oxide catalyst into a muffle furnace for calcination, the calcination temperature is 450 degrees centigrade, and the calcination time is 4 hours. Put the calcined magnesium oxide powder into a 1000 ml flask, add 500 ml of deionized water at a temperature of 80 degrees Celsius, and stir for 1 hour at a constant temperature of 80 degrees Celsius in a water bath. Then at a constant temperature of 80 degrees Celsius, the stirring speed was adjusted to 400 rpm, and carbon dioxide gas was introduced into the slurry, and the flow control of carbon dioxide was 100 milliliters per minute. Stirring was continued for 4 hours, and then the slurry was filtered with a vacuum pump to obtain a filter cake. The filter cake was dried in a drying oven at 80 degrees Celsius for 10 ...
Embodiment 2
[0031] Weigh 60 grams of spent magnesia catalyst, dry it at 80 degrees centigrade, put it into a ball mill and pulverize it to more than 80 mesh. Put the pulverized spent magnesium oxide catalyst into a muffle furnace for calcination, the calcination temperature is 500 degrees centigrade, and the calcination time is 4 hours. Put the calcined magnesium oxide powder into a 1000 ml flask, add 600 ml of deionized water at a temperature of 80 degrees Celsius, and stir for 1 hour at a constant temperature of 80 degrees Celsius in a water bath. Then at a constant temperature of 80 degrees Celsius, the stirring speed was adjusted to 300 revolutions per minute, and carbon dioxide gas was introduced into the slurry, and the flow control of carbon dioxide was 200 milliliters per minute. Stirring was continued for 6 hours, and then the slurry was filtered with a vacuum pump to obtain a filter cake. The filter cake was dried in a drying oven at 80 degrees Celsius for 10 hours to obtain a ...
PUM
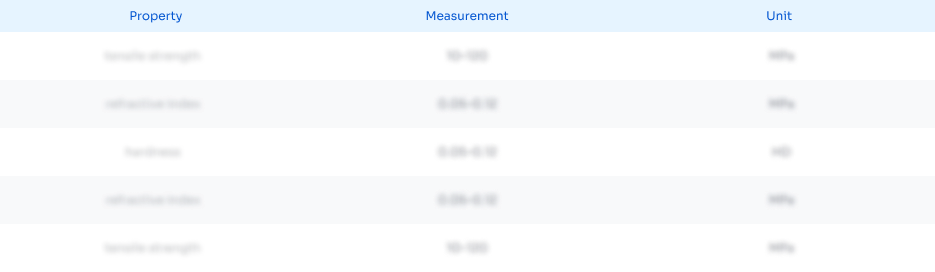
Abstract
Description
Claims
Application Information

- R&D
- Intellectual Property
- Life Sciences
- Materials
- Tech Scout
- Unparalleled Data Quality
- Higher Quality Content
- 60% Fewer Hallucinations
Browse by: Latest US Patents, China's latest patents, Technical Efficacy Thesaurus, Application Domain, Technology Topic, Popular Technical Reports.
© 2025 PatSnap. All rights reserved.Legal|Privacy policy|Modern Slavery Act Transparency Statement|Sitemap|About US| Contact US: help@patsnap.com