High-sulfur-resistance metal sulfate denitration catalyst and preparation method thereof
A metal sulfate and denitrification catalyst technology, applied in chemical instruments and methods, physical/chemical process catalysts, separation methods, etc., can solve the problems of reduced catalytic efficiency of catalysts, and achieve suitable promotion and use, high SCR activity, and avoid deposition Effect
- Summary
- Abstract
- Description
- Claims
- Application Information
AI Technical Summary
Problems solved by technology
Method used
Image
Examples
Embodiment 1
[0029] A method for preparing a metal sulfate denitration catalyst with high sulfur resistance, adopting a rotary evaporation impregnation method to prepare the metal sulfate denitration catalyst, comprising the following steps:
[0030] a. Take by weighing 0.02g of copper sulfate, place it in a 100ml round-bottomed flask, measure 70ml of deionized water with a measuring cylinder and pour it into the round-bottomed flask, place the round-bottomed flask in an ultrasonic machine, and ultrasonically disperse it evenly to obtain Metal sulfate solution;
[0031] b. Weigh 2g of silicon oxide and place it in the metal sulfate solution of the round-bottomed flask, and ultrasonicate the mixed solution again to form a uniform suspension; place the round-bottomed flask on a rotary evaporator, In the process of water bath at ℃, carry out rotary evaporation to obtain the catalyst precursor;
[0032] c. Place the obtained catalyst precursor in an oven at 60°C and dry it for 12 hours. The d...
Embodiment 2
[0038] This embodiment is basically the same as Embodiment 1, and the special features are:
[0039] A method for preparing a metal sulfate denitration catalyst with high sulfur resistance, adopting a rotary evaporation impregnation method to prepare the metal sulfate denitration catalyst, comprising the following steps:
[0040] Weigh 0.15g of copper sulfate and place it in a 100ml round bottom flask, measure 70ml of ethanol with a graduated cylinder and pour it into the round bottom flask, place the round bottom flask in an ultrasonic machine to disperse evenly, then weigh 2g of silicon oxide Place in the metal sulfate solution in a round bottom flask and sonicate again to form a homogeneous suspension. The round-bottomed flask was placed on a rotary evaporator and rotated in a water bath at 45 °C to obtain the catalyst precursor.
[0041] The obtained catalyst precursor was dried in an oven at 80°C for 6 hours. The dried catalyst precursor was fully ground and passed throu...
Embodiment 3
[0046] This embodiment is basically the same as the previous embodiment, and the special features are:
[0047] A method for preparing a metal sulfate denitration catalyst with high sulfur resistance, adopting a rotary evaporation impregnation method to prepare the metal sulfate denitration catalyst, comprising the following steps:
[0048] Weigh 0.2g of copper sulfate and place it in a 100ml round bottom flask, use a graduated cylinder to measure 70ml of isopropanol and pour it into the round bottom flask, place the round bottom flask in an ultrasonic machine to disperse evenly, then weigh 2g of Zirconia is placed in the metal sulfate solution in a round bottom flask and sonicated again to form a homogeneous suspension. The round-bottomed flask was placed on a rotary evaporator and rotated in a water bath at 50 °C to obtain the catalyst precursor.
[0049] The obtained catalyst precursor was dried in an oven at 60°C for 2 hours. The dried catalyst precursor was fully ground ...
PUM
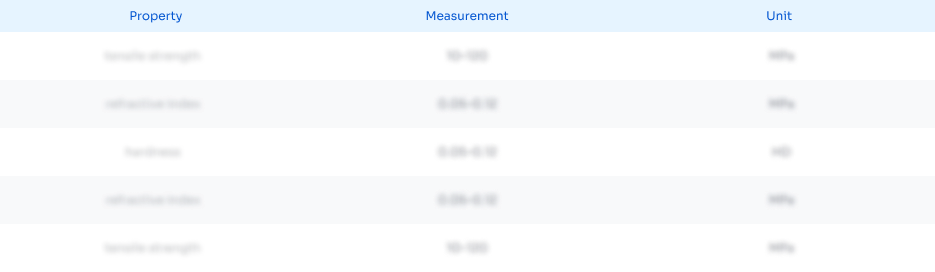
Abstract
Description
Claims
Application Information

- R&D
- Intellectual Property
- Life Sciences
- Materials
- Tech Scout
- Unparalleled Data Quality
- Higher Quality Content
- 60% Fewer Hallucinations
Browse by: Latest US Patents, China's latest patents, Technical Efficacy Thesaurus, Application Domain, Technology Topic, Popular Technical Reports.
© 2025 PatSnap. All rights reserved.Legal|Privacy policy|Modern Slavery Act Transparency Statement|Sitemap|About US| Contact US: help@patsnap.com