Manufacturing process of cooling type grain-grain viscose fiber and product
A production process and fiber technology, which is applied in the field of composite fiber production technology, can solve the problems of increasing the manufacturing difficulty, increasing the manufacturing cost, and the effect is not obvious, and achieving the effect of reducing the manufacturing difficulty, being easy to operate, and not difficult to operate.
- Summary
- Abstract
- Description
- Claims
- Application Information
AI Technical Summary
Problems solved by technology
Method used
Image
Examples
Embodiment 1
[0055] see figure 1 — Figure 7 , a kind of manufacturing process of cooling formula granular viscose fiber, comprises the following steps:
[0056] The first step: first use the fiber filaments to make the core yarn 1, and then attach a colloidal liquid to the outer surface of the core yarn 1 to obtain the viscous core yarn 11; the colloidal liquid is an adhesive, acetic acid spinning solution or viscose Spinning solution; the fiber silk is viscose fiber, cotton fiber, hemp fiber, chitin fiber, alginate fiber, chitosan fiber, polyvinyl alcohol fiber, polycaprolactone fiber, polyglycolic acid ester fiber any one or any combination of
[0057] The second step: first pass the viscous core yarn 11 through the powder area 2, and a plurality of PLA powder particles 3 are arranged in the powder area 2. When passing through, the PLA powder particles 3 are combined with the outer surface of the viscous core yarn 11. , to obtain powdered yarn 12; the binder is any one of pectin, pol...
Embodiment 2
[0061] Basic content is the same as embodiment 1, the difference is:
[0062] Said passing the viscous core yarn 11 from the powder area 2 refers to passing the viscous core yarn 11 axially through the powder sticking cylinder 4, which includes a front cylinder cover 41, a middle cylinder body 42, and a rear cylinder arranged in sequence. Cover 43, the two ends of the middle cylinder body 42 are respectively sealed and connected with the front cylinder cover 41 and the rear cylinder cover 43. The front cylinder cover 41 and the rear cylinder cover 43 are respectively provided with a yarn inlet hole 411 and a yarn outlet hole 431. The inside of the cylinder body 42 is a middle cylinder chamber 421, and the side circumference of the middle cylinder body 42 is provided with a plurality of powder inlets 44 communicating with the middle cylinder chamber 421. A front empty area 45 and a rear empty area 46 are respectively clamped between the cylinder covers 43;
[0063] When the vi...
Embodiment 3
[0065] Basic content is the same as embodiment 1, the difference is:
[0066] The arrangement area 441 is set lower than the viscous core yarn 11 ; the arrangement structure of the powder inlets 44 is: there are at least two rows, and each row includes at least two powder inlets 44 . When the viscous core yarn 11 passes through the powder sticking cylinder 4, the viscous core yarn 11 rotates while moving in the axial direction.
PUM
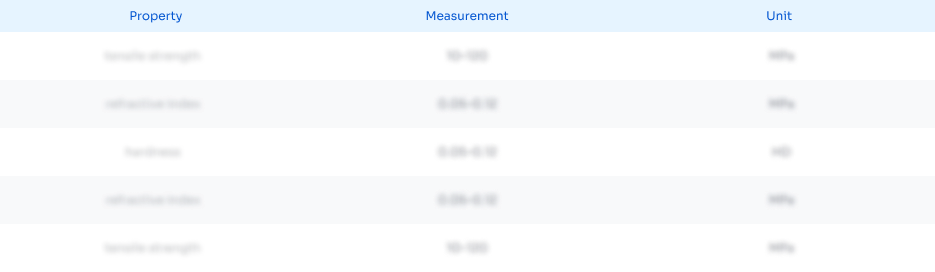
Abstract
Description
Claims
Application Information

- Generate Ideas
- Intellectual Property
- Life Sciences
- Materials
- Tech Scout
- Unparalleled Data Quality
- Higher Quality Content
- 60% Fewer Hallucinations
Browse by: Latest US Patents, China's latest patents, Technical Efficacy Thesaurus, Application Domain, Technology Topic, Popular Technical Reports.
© 2025 PatSnap. All rights reserved.Legal|Privacy policy|Modern Slavery Act Transparency Statement|Sitemap|About US| Contact US: help@patsnap.com