Anti-corrosion process for iron handrail
An anti-corrosion and railing technology, applied in anti-corrosion coatings, devices for coating liquid on the surface, coatings, etc., can solve the problems of poor uniformity of spraying, poor corrosion resistance, waste of cleaning agents, etc., and achieve easy portability and anti-corrosion The effect of long time and avoiding the use of large devices
- Summary
- Abstract
- Description
- Claims
- Application Information
AI Technical Summary
Problems solved by technology
Method used
Image
Examples
Embodiment 1
[0026] Such as figure 1 As shown, the present invention provides a spray cleaning device, including a liquid storage tank 1, a submersible pump 2 is installed inside the liquid storage tank 1, and the submersible pump 2 is connected to a power supply; the submersible pump 2 is connected with an outlet pipe 3, and the outlet pipe 3 passes through The telescopic pipe 4 is connected with an atomizing nozzle; the water outlet pipe 3 and the telescopic pipe 4 are detachably connected;
[0027] A bristle 5 is installed on the atomizing nozzle, and the bristle 5 is distributed on the spray surface of the atomizing nozzle; the bristle 5 is a steel wire;
[0028] A storage box 6 is installed on the liquid storage box 1, the outlet pipe 3 penetrates into the storage box 6, and is connected with the telescopic tube 4 in the storage box 6; a hollow frame 7 is arranged on the top surface of the storage box 6, and the telescopic tube 4 passes through The hollow frame 7 is connected to the ...
Embodiment 2
[0031] A kind of antirust paint comprises the component of following parts by weight:
[0032] 45 parts of water-based acrylic resin, 4.5 parts of phosphate pigment, 20 parts of filler, 7 parts of alcohol ether ester coalescent, 0.6 part of methyl methacrylate, 0.4 part of butyl methacrylate, 22.5 parts of distilled water.
[0033] The preparation process of above-mentioned antirust paint is as follows:
[0034] Mix the water-based acrylic resin, methyl methacrylate and butyl methacrylate, and keep stirring under the condition of 1000r / min to obtain the mixed solution I, which is ready for use;
[0035] Mix phosphate pigments, fillers and distilled water, stir to form a suspension, pour into the mixed solution I, continue to stir until uniform, then add alcohol ether ester film-forming aids to it, and mix well to obtain an antirust paint.
Embodiment 3
[0037] A kind of antirust paint comprises the component of following parts by weight:
[0038] 40 parts of water-based acrylic resin, 6 parts of phosphate pigment, 15 parts of filler, 10 parts of alcohol ether ester coalescent, 0.5 part of methyl methacrylate, 0.5 part of butyl methacrylate, 28 parts of distilled water.
PUM
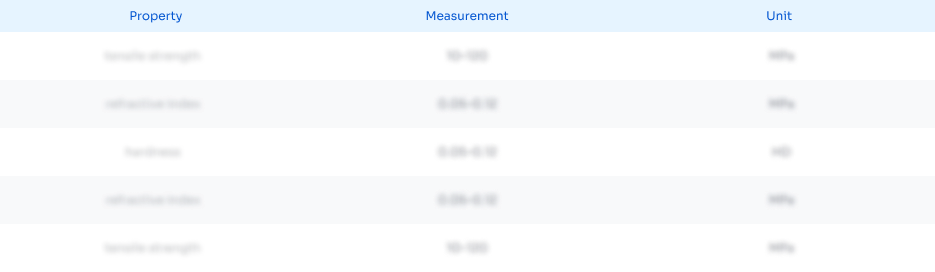
Abstract
Description
Claims
Application Information

- Generate Ideas
- Intellectual Property
- Life Sciences
- Materials
- Tech Scout
- Unparalleled Data Quality
- Higher Quality Content
- 60% Fewer Hallucinations
Browse by: Latest US Patents, China's latest patents, Technical Efficacy Thesaurus, Application Domain, Technology Topic, Popular Technical Reports.
© 2025 PatSnap. All rights reserved.Legal|Privacy policy|Modern Slavery Act Transparency Statement|Sitemap|About US| Contact US: help@patsnap.com