Ultra-precision hydraulic control method
A control method and ultra-precise technology, applied in the direction of fluid pressure actuation device, fluid pressure actuation system test, fluid pressure actuation system components, etc., can solve the problem that higher precision is difficult to achieve, output precision is not high enough, and interference factors Many problems are solved to achieve the effects of accurate pressure measurement and temperature detection and control, good voltage regulation effect and low interference factor.
- Summary
- Abstract
- Description
- Claims
- Application Information
AI Technical Summary
Problems solved by technology
Method used
Image
Examples
Embodiment Construction
[0026] The ultra-precise hydraulic control circuit includes the oil supply circuit, oil return circuit and cooling circuit respectively connected to the oil tank 1;
[0027] Such as figure 1 , including an oil supply circuit, an oil return circuit, and a cooling circuit respectively connected to the oil tank 1;
[0028] Wherein, the oil supply circuit includes: a hydraulic pump 11 driven by the first servo motor 10, a pressure reducing valve, an accumulator, an overflow valve 14, and a high-pressure oil filter. The oil suction port of the hydraulic pump 11 is connected to the oil tank 1, and the outlet of the hydraulic pump 11 is connected to The high-pressure oil filter 13, the outlet of the high-pressure oil filter 13 is connected to the overflow valve 14, the oil return of the overflow valve 14 is connected to the oil tank 1, the accumulator includes a first accumulator 16 and a second accumulator 18, and the pressure reducing valve includes : the first pressure reducing v...
PUM
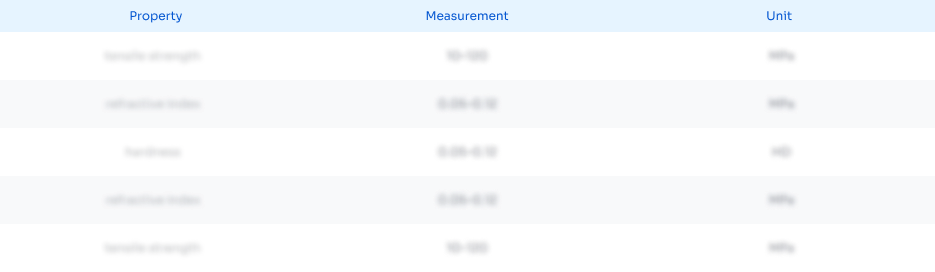
Abstract
Description
Claims
Application Information

- R&D Engineer
- R&D Manager
- IP Professional
- Industry Leading Data Capabilities
- Powerful AI technology
- Patent DNA Extraction
Browse by: Latest US Patents, China's latest patents, Technical Efficacy Thesaurus, Application Domain, Technology Topic, Popular Technical Reports.
© 2024 PatSnap. All rights reserved.Legal|Privacy policy|Modern Slavery Act Transparency Statement|Sitemap|About US| Contact US: help@patsnap.com