Polyethylene composite antibacterial coating and preparation method thereof
A composite antibacterial and polyethylene technology, which is applied in coatings, antifouling/underwater coatings, devices for coating liquids on surfaces, etc., can solve problems such as shedding, pollution, and loss of antibacterial properties
- Summary
- Abstract
- Description
- Claims
- Application Information
AI Technical Summary
Problems solved by technology
Method used
Image
Examples
Embodiment 1
[0037] (1) Preparation of coating:
[0038] Take 16 parts of polyethylene glycol and 21 parts of acrylic acid, add deionized water, and stir at room temperature for 10 minutes to prepare a mixed solution;
[0039] Dissolve 100 parts of polyethylene in N,N-dimethylformamide, add N,N'-methylenebisacrylamide, stir at 70°C for 10 minutes, insert electrodes, and electrify for 5 minutes, where the discharge voltage is 600V and the current 60mV, then react at a constant temperature of 70°C for 4h, take the reaction product and wash and dry it to obtain modified polyethylene;
[0040] Take modified polyethylene and 8 parts of chloroether resin, add xylene and stir thoroughly to prepare the coating;
[0041] (2) Preparation of surface treatment agent:
[0042] (a) Preparation of modified zinc oxide nanocolumns:
[0043] Take the glass sheet for full cleaning and drying as the substrate;
[0044] Blend polyvinyl alcohol and zinc acetate, add deionized water, heat to 80°C and stir fo...
Embodiment 2
[0057] (1) Preparation of coating:
[0058] Take 18 parts of polyethylene glycol and 24 parts of acrylic acid, add deionized water, and stir at room temperature for 15 minutes to prepare a mixed solution;
[0059] Dissolve 100 parts of polyethylene in N,N-dimethylformamide, add N,N'-methylenebisacrylamide, stir at 75°C for 15 minutes, insert electrodes, and electrify for 7 minutes, in which the discharge voltage is 635V and the current 66mV, then react at a constant temperature of 75°C for 4.5h, take the reaction product and wash and dry it to obtain modified polyethylene;
[0060] Take modified polyethylene and 11 parts of chloroether resin, add xylene and stir thoroughly to prepare the coating;
[0061] (2) Preparation of surface treatment agent:
[0062] (a) Preparation of modified zinc oxide nanocolumns:
[0063] Take the glass sheet for full cleaning and drying as the substrate;
[0064] Blend polyvinyl alcohol and zinc acetate, add deionized water, heat to 87°C and s...
Embodiment 3
[0077] (1) Preparation of coating:
[0078] Take 20 parts of polyethylene glycol and 28 parts of acrylic acid, add deionized water, and stir at room temperature for 20 minutes to prepare a mixed solution;
[0079] Dissolve 100 parts of polyethylene in N,N-dimethylformamide, add N,N'-methylenebisacrylamide, stir at 80°C for 20 minutes, insert electrodes, and electrify for 10 minutes, where the discharge voltage is 670V and the current 72mV, then reacted at a constant temperature of 80°C for 5h, and the reaction product was washed and dried to obtain modified polyethylene;
[0080] Take modified polyethylene and 15 parts of chloroether resin, add xylene and stir thoroughly to prepare the coating;
[0081] (2) Preparation of surface treatment agent:
[0082] (a) Preparation of modified zinc oxide nanocolumns:
[0083] Take the glass sheet for full cleaning and drying as the substrate;
[0084] Blend polyvinyl alcohol and zinc acetate, add deionized water, heat to 95°C and sti...
PUM
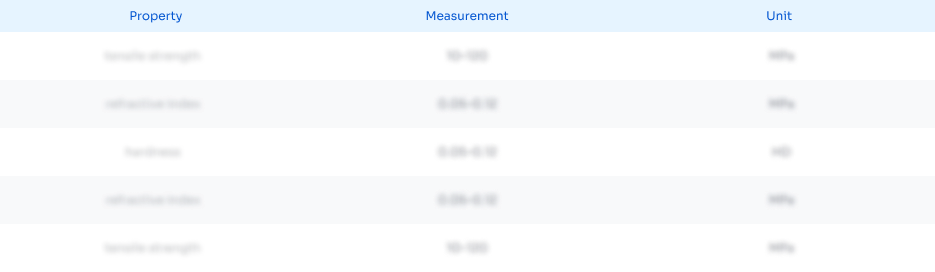
Abstract
Description
Claims
Application Information

- R&D Engineer
- R&D Manager
- IP Professional
- Industry Leading Data Capabilities
- Powerful AI technology
- Patent DNA Extraction
Browse by: Latest US Patents, China's latest patents, Technical Efficacy Thesaurus, Application Domain, Technology Topic, Popular Technical Reports.
© 2024 PatSnap. All rights reserved.Legal|Privacy policy|Modern Slavery Act Transparency Statement|Sitemap|About US| Contact US: help@patsnap.com