Energy-saving thermal cracking reaction kettle for treating organic solid wastes
A pyrolysis reactor and organic solid technology, applied in coke oven heating, dry distillation gas discharge device, direct and indirect heating combined dry distillation, etc., can solve the problems of low efficiency of heat energy utilization, and improve energy utilization efficiency, The effect of increasing the heat exchange area
- Summary
- Abstract
- Description
- Claims
- Application Information
AI Technical Summary
Problems solved by technology
Method used
Image
Examples
Embodiment 1
[0089] In the present invention, as figure 1 As shown, the reactor inner cylinder 20 of the horizontal thermal cracking reactor is placed inside the reactor outer cylinder 14 . A part of both the feed end 10 of the reactor and the outlet port 29 of the reactor is located inside the outer cylinder 14 of the reactor, and the other part is located outside the outer cylinder 14 of the reactor. The feed end 10 of the reactor in Figure 1, the cylinder body 20 of the reactor, the outlet port 29 of the reactor, the waste materials filled in the reactor, the stirring mechanism of the reactor and the weight of the U-shaped pipe member are supported by four groups of supporting wheels. It is supported by supporting wheel bracket seat 8 and some hot blast inlet support pillars 7 and support frame body 35; the weight of reactor outer cylinder body 14 is supported by several outer cylinder body support frames 15; hot blast channel 22 is reactor outer cylinder body 14 The space between the ...
PUM
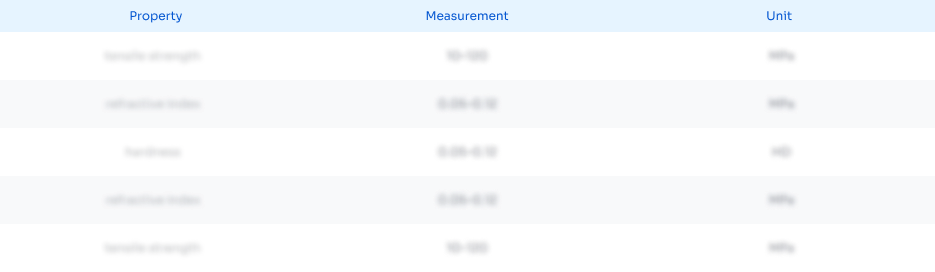
Abstract
Description
Claims
Application Information

- R&D
- Intellectual Property
- Life Sciences
- Materials
- Tech Scout
- Unparalleled Data Quality
- Higher Quality Content
- 60% Fewer Hallucinations
Browse by: Latest US Patents, China's latest patents, Technical Efficacy Thesaurus, Application Domain, Technology Topic, Popular Technical Reports.
© 2025 PatSnap. All rights reserved.Legal|Privacy policy|Modern Slavery Act Transparency Statement|Sitemap|About US| Contact US: help@patsnap.com