Defoaming type polycarboxylate superplasticizer and preparation method thereof
A technology of water reducing agent and polycarboxylic acid, applied in the field of defoaming type polycarboxylic acid water reducing agent and its preparation, can solve the problems of poor compatibility, poor placement stability, poor effect of controlling gas content, etc.
- Summary
- Abstract
- Description
- Claims
- Application Information
AI Technical Summary
Problems solved by technology
Method used
Image
Examples
preparation example Construction
[0030] The invention provides a preparation method of a defoaming polycarboxylate water reducer, which specifically comprises the following steps:
[0031] 1. Preparation of the first polymer:
[0032] In terms of weight fractions, 300-400 parts by weight of unsaturated polyoxyethylene ether monomer with a molecular weight of 600-3000, 5.0-20.0 parts by weight of acrylate monomer, 1.0-3.0 parts by weight of oxidant and 200-260 parts by weight Parts of water are mixed and heated to obtain solution A;
[0033] 30.0-60.0 parts by weight of unsaturated carboxylic acid, 0.3-3.0 parts by weight of reducing agent and 150-220 parts by weight of water are formulated into solution B;
[0034] 1.0-4.0 parts by weight of chain transfer agent and 20-30 parts by weight of water are formulated into solution C;
[0035] Put solution A in a 250ml four-neck flask, stir and heat to 40-65°C, add solution B and solution C dropwise into solution A respectively, the dropping time is 1.5-3 hours, k...
Embodiment 1
[0045] 1. Preparation of the first polymer:
[0046] 350 parts by weight of methallyl polyoxyethylene ether with a molecular weight of 2500, 15.0 parts by weight of methyl acrylate, 2.3 parts by weight of oxidant ammonium persulfate and 220 parts by weight of water were mixed and heated to obtain solution A;
[0047] 45.0 parts by weight of crotonic acid and 1.3 parts by weight of reducing agent sodium formaldehyde sulfoxylate and water of 190 parts by weight are made into solution B;
[0048] The chain transfer agent mercaptoethanol of 3.0 parts by weight and the water of 25 parts by weight are made into solution C;
[0049] Put solution A in a 250ml four-neck flask, stir and heat to 60°C, add solution B and solution C dropwise into solution A respectively, the dropping time is 2h, keep warm for 1.5h after the dropping, and carry out the copolymerization reaction; The pH value is adjusted to 6.0 and the solid content is adjusted to 40% by using liquid caustic soda with a mas...
Embodiment 2
[0055] 1. Preparation of the first polymer:
[0056] 300 parts by weight of allyl polyoxyethylene ether with a molecular weight of 1000, 8.0 parts by weight of methyl acrylate, 1.5 parts by weight of oxidant hydrogen peroxide and 200 parts by weight of water were mixed and heated to obtain solution A;
[0057] 30.0 parts by weight of acrylic acid, 0.5 parts by weight of reducing agent ascorbic acid and 150 parts by weight of water are formulated into solution B;
[0058] The chain transfer agent thioglycolic acid of 1.5 parts by weight and the water of 20 parts by weight are made into solution C;
[0059] Put solution A in a 250ml four-neck flask, stir and heat to 50°C, add solution B and solution C dropwise to solution A respectively, the dropping time is 1.5h, keep warm for 1h after the dropping, and carry out the copolymerization reaction; The pH value is adjusted to 6.5 with 30-32% mass concentration of liquid caustic soda, and the solid content is adjusted to 40%. A fir...
PUM
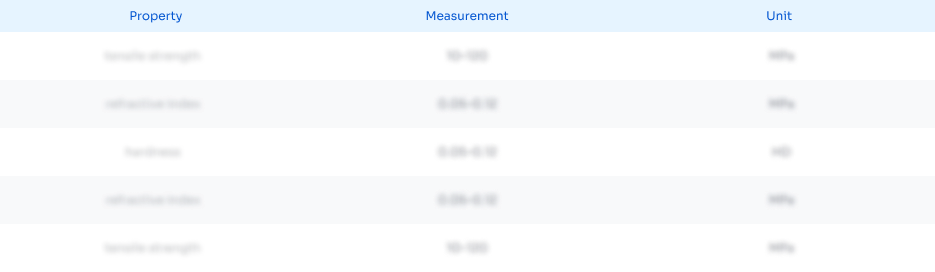
Abstract
Description
Claims
Application Information

- R&D
- Intellectual Property
- Life Sciences
- Materials
- Tech Scout
- Unparalleled Data Quality
- Higher Quality Content
- 60% Fewer Hallucinations
Browse by: Latest US Patents, China's latest patents, Technical Efficacy Thesaurus, Application Domain, Technology Topic, Popular Technical Reports.
© 2025 PatSnap. All rights reserved.Legal|Privacy policy|Modern Slavery Act Transparency Statement|Sitemap|About US| Contact US: help@patsnap.com