Variable stiffness tuned piezoelectric energy harvester
A piezoelectric energy harvesting and variable stiffness technology, which is applied in the field of energy harvesting, can solve the problems of narrow applicable frequency band of vibration and noise reduction components, heavy structural weight, and failure to realize vibration mechanical energy recovery and utilization.
- Summary
- Abstract
- Description
- Claims
- Application Information
AI Technical Summary
Problems solved by technology
Method used
Image
Examples
Embodiment Construction
[0026] In order to express the structural principles and working methods in the examples of the present invention more intuitively and clearly, the following will introduce the embodiments in conjunction with the relevant drawings. Apparently, the described embodiments are only part of the embodiments of the present invention. Based on the embodiments of the present invention, all other embodiments obtained by persons of ordinary skill in the art without making creative efforts belong to the protection scope of the present invention.
[0027] Such as figure 1 As shown, the piezoelectric energy harvester in the present invention includes a variable stiffness tuning module and a piezoelectric energy harvesting module, wherein the variable stiffness tuning module includes a base 1, a piezoelectric ceramic block 2, a T-shaped hinge 3, and a stiffness adjustment ring 4 , Crank slider compliance mechanism 5, adjusting screw 6, gasket 7. By turning the adjusting screw 6, the piezoel...
PUM
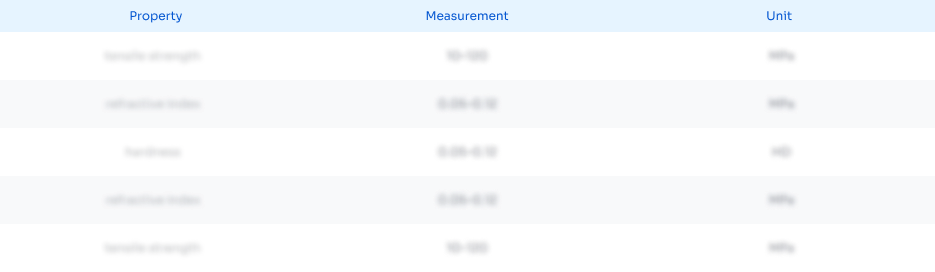
Abstract
Description
Claims
Application Information

- Generate Ideas
- Intellectual Property
- Life Sciences
- Materials
- Tech Scout
- Unparalleled Data Quality
- Higher Quality Content
- 60% Fewer Hallucinations
Browse by: Latest US Patents, China's latest patents, Technical Efficacy Thesaurus, Application Domain, Technology Topic, Popular Technical Reports.
© 2025 PatSnap. All rights reserved.Legal|Privacy policy|Modern Slavery Act Transparency Statement|Sitemap|About US| Contact US: help@patsnap.com