Three-stage phase change heat exchanger
A technology of phase-change heat exchangers and heat exchangers, which is applied in the types of heat exchangers, indirect heat exchangers, heat storage equipment, etc., and can solve problems such as dryness, inability to transfer in time, and rising gas content of working fluids
- Summary
- Abstract
- Description
- Claims
- Application Information
AI Technical Summary
Problems solved by technology
Method used
Image
Examples
Embodiment 1
[0045] Such as Figure 4 As shown, the heat dissipation system for high-power components and parts according to an embodiment of the present invention includes a three-stage phase-change heat exchanger (1), high-power components and parts (2), a radiator (3), a liquid storage tank according to the present invention (4), fluorine pump (5), coolant supply system and connecting pipelines. According to a specific embodiment of the present invention, the phase-change material is selected as a phase-change metal material with a low melting point of 48°C, and is filled between the heat-conducting ribs (2-1). Driven by the fluorine pump, the refrigerant enters the three-stage phase-change heat exchanger, absorbs the heat released by the high-power components (2), changes from single-phase to gas-liquid two-phase, and then enters the radiator to dissipate heat, and the refrigerant returns to single-phase phase state, then enters the liquid storage tank, and is finally pumped away by t...
Embodiment 2
[0047] Such as Figure 5As shown, the heat dissipation system for high-power components and parts according to an embodiment of the present invention includes a three-stage phase-change heat exchanger (1), high-power components and parts (2), a radiator (3), a liquid storage tank according to the present invention (4), fluorine pump (5) coolant supply and recovery system (7) and connecting pipelines. According to a specific embodiment of the present invention, the phase-change material is selected as a phase-change metal material with a low melting point of 48°C, and is filled between the heat-conducting ribs (2-1). Driven by the fluorine pump, the refrigerant enters the three-stage phase-change heat exchanger, absorbs the heat released by the high-power components (2), changes from single-phase to gas-liquid two-phase, and then enters the radiator to dissipate heat, and the refrigerant returns to single-phase phase state, then enters the liquid storage tank, and is finally p...
PUM
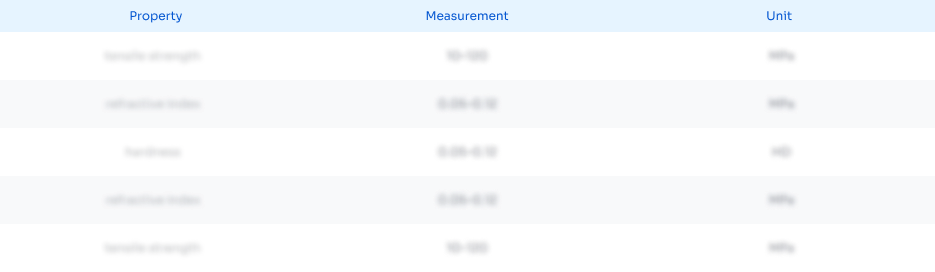
Abstract
Description
Claims
Application Information

- R&D
- Intellectual Property
- Life Sciences
- Materials
- Tech Scout
- Unparalleled Data Quality
- Higher Quality Content
- 60% Fewer Hallucinations
Browse by: Latest US Patents, China's latest patents, Technical Efficacy Thesaurus, Application Domain, Technology Topic, Popular Technical Reports.
© 2025 PatSnap. All rights reserved.Legal|Privacy policy|Modern Slavery Act Transparency Statement|Sitemap|About US| Contact US: help@patsnap.com