A kind of oil-water type bentonite-polyurea composite grease composition and preparation method thereof
A technology of grease composition and bentonite grease, which is applied in the field of grease, can solve problems such as low consistency, service temperature, and poor lubricity, and achieve the effects of low cost, stable performance, and good cooling effect
- Summary
- Abstract
- Description
- Claims
- Application Information
AI Technical Summary
Problems solved by technology
Method used
Image
Examples
preparation example ---
[0105] Preparation Example---Preparation of Polyurea Grease
[0106] 400g PAO4 lubricating base oil (100℃ kinematic viscosity is 4mm 2 / s) Stir and heat up, heat up to 52-55°C, add 33g of octadecylamine and 12g of cyclohexylamine, stir for 30min, add 34g of diphenylmethane diisocyanate at 70-80°C to react for 30min, continue to heat up the reaction to 205°C Stop heating, keep the temperature for 15min, pour 150g PAO4, cool down to 130℃, add 4g extreme pressure antiwear agent and 1g rust inhibitor, stir for 30min, grind and homogenize to obtain polyurea grease.
Embodiment 1
[0108] Add 4g of polyethylene glycol 2000 to 36g of water, keep the temperature at 20°C, stir well, and dissolve completely to obtain a mixed solution. Then 27 g of organic amine modified montmorillonite was added to the mixture, and stirred for 15 min. Then slowly add 3g of propylene carbonate in a thin stream, stir well for 30min, and then add 30g of PAO4 lubricating base oil (kinematic viscosity at 100°C is 4mm 2 / s), continue to heat up to 60° C., stir for 15 minutes, add 400 g of polyurea grease after stirring evenly, grind and homogenize to obtain oil-water bentonite-polyurea composite grease. The physicochemical properties of the obtained lipids are shown in Table 1.
[0109] The percentage of each component used for preparing the oil-water type bentonite-polyurea compound grease is: polyethylene glycol: 0.8%; water: 7.2%; PAO 4: 6%; bentonite: 5.4%; propylene carbonate: 0.6%; Polyurea Grease: 80%.
Embodiment 2
[0111] Add 4g of polyethylene glycol 2000 to 36g of water, keep the temperature at 20°C, stir well, and dissolve completely to obtain a mixed solution. Then 20 g of organic amine modified montmorillonite was added to the mixed solution, and stirred for 15 min. Then slowly add 5g of propylene carbonate in a thin stream, stir well for 30min, and then add 35g of PAO4 lubricating base oil (kinematic viscosity at 100°C is 4mm 2 / s), continue to heat up to 60° C., stir for 15 minutes, add 100 g of polyurea grease after stirring evenly, grind and homogenize to obtain oil-water bentonite-polyurea composite grease. The physicochemical properties of the obtained lipids are shown in Table 1.
[0112] The percentage of each component used for preparing the oil-water type bentonite-polyurea compound grease is: polyethylene glycol: 2%; water: 18%; PAO 4: 17.5%; bentonite: 10%; propylene carbonate: 2.5%; Polyurea Grease: 50%.
PUM
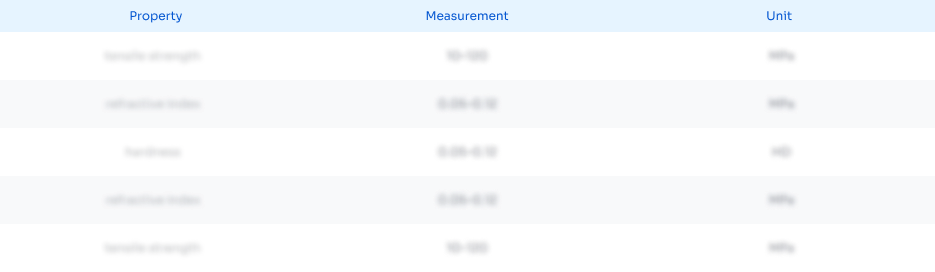
Abstract
Description
Claims
Application Information

- R&D
- Intellectual Property
- Life Sciences
- Materials
- Tech Scout
- Unparalleled Data Quality
- Higher Quality Content
- 60% Fewer Hallucinations
Browse by: Latest US Patents, China's latest patents, Technical Efficacy Thesaurus, Application Domain, Technology Topic, Popular Technical Reports.
© 2025 PatSnap. All rights reserved.Legal|Privacy policy|Modern Slavery Act Transparency Statement|Sitemap|About US| Contact US: help@patsnap.com