Chemical pressure vessel manufacturing and forming process
A pressure vessel and molding process technology, which is applied in the field of chemical pressure vessel manufacturing and molding technology, can solve the problem of butt joint dislocation between the pressure vessel cylinder and the pressure vessel head, the inability to clamp and position the pressure vessel cylinder, and reduce the pressure vessel cylinder and pressure vessel. Problems such as the quality of the butt joint of the pressure vessel head
- Summary
- Abstract
- Description
- Claims
- Application Information
AI Technical Summary
Problems solved by technology
Method used
Image
Examples
Embodiment Construction
[0032] The embodiments of the present invention will be described in detail below with reference to the accompanying drawings, but the present invention can be implemented in many different ways defined and covered by the claims.
[0033] Such as Figure 1 to Figure 7 As shown, a chemical pressure vessel manufacturing molding process mainly includes the following steps:
[0034] Step 1, material preparation, prepare the raw materials required for chemical pressure vessels, and obtain the raw materials for pressure vessels;
[0035] Step 2, rolling operation, performing rolling operation on the pressure vessel raw material obtained in step 1, to obtain the rolled pressure vessel cylinder and pressure vessel head;
[0036] Step 3, assembly operation, place the rolled pressure vessel cylinder and pressure vessel head obtained in step 2 into the pressure vessel assembly equipment for assembly operation, and obtain the assembled pressure vessel;
[0037] Step 4, welding operation...
PUM
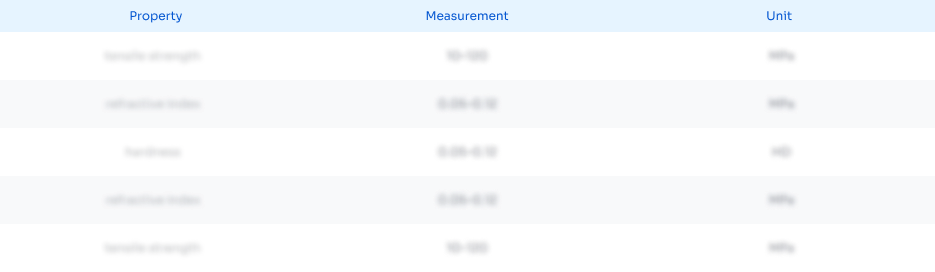
Abstract
Description
Claims
Application Information

- R&D Engineer
- R&D Manager
- IP Professional
- Industry Leading Data Capabilities
- Powerful AI technology
- Patent DNA Extraction
Browse by: Latest US Patents, China's latest patents, Technical Efficacy Thesaurus, Application Domain, Technology Topic, Popular Technical Reports.
© 2024 PatSnap. All rights reserved.Legal|Privacy policy|Modern Slavery Act Transparency Statement|Sitemap|About US| Contact US: help@patsnap.com