Real-time winding forming device for soft grain core mold explosive-carrying composite shell
A technology of winding forming and casing, applied in the field of solid rocket motors, can solve the problems of deformation of the soft grain core mold and changing section of the outer casing of the engine, and achieve the effects of simplifying the production process, shortening the processing cycle, and reducing the production cost.
- Summary
- Abstract
- Description
- Claims
- Application Information
AI Technical Summary
Problems solved by technology
Method used
Image
Examples
Embodiment 1
[0043] In a specific embodiment of the present invention, a closed-loop molding control system of the composite shell is adopted to integrally form and wind a compound shell with medicine of a flexible cross-section mandrel with a diameter of 300 mm and a length of 1000 mm. This embodiment solves the problem of insufficient rigidity of the mandrel when the viscoelastic grain acts as the mandrel for winding, and the problem of easy deformation during the belt tension winding process that causes the size change of the winding layer, as well as the problem of the integrated molding of the engine outer shell structure. The problem of variable cross-section improves the fine control of product quality.
PUM
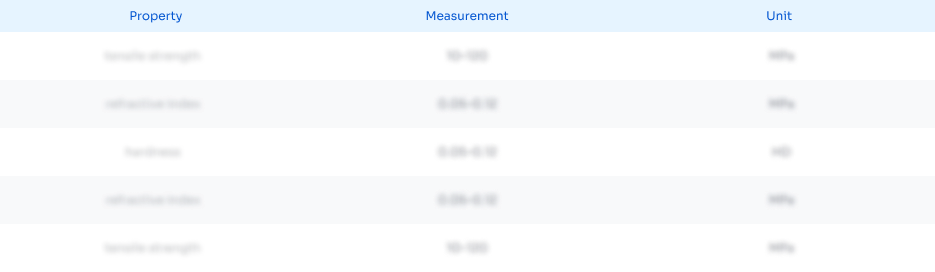
Abstract
Description
Claims
Application Information

- R&D
- Intellectual Property
- Life Sciences
- Materials
- Tech Scout
- Unparalleled Data Quality
- Higher Quality Content
- 60% Fewer Hallucinations
Browse by: Latest US Patents, China's latest patents, Technical Efficacy Thesaurus, Application Domain, Technology Topic, Popular Technical Reports.
© 2025 PatSnap. All rights reserved.Legal|Privacy policy|Modern Slavery Act Transparency Statement|Sitemap|About US| Contact US: help@patsnap.com