Iron ore powder liquid phase fluidity detection method based on sintering actual production conditions
A liquid phase fluidity and detection method technology, which is applied in the field of ironmaking and sintering, can solve the problems of matching, increasing the effective contact area, liquid phase generation and flow ductility interference, etc., and achieves low test cost, easy operation, and equipment simple effect
- Summary
- Abstract
- Description
- Claims
- Application Information
AI Technical Summary
Problems solved by technology
Method used
Image
Examples
Embodiment
[0023] The general idea and implementation steps of the embodiment are as follows:
[0024] 1) Preliminary preparation: draw equidistant grid lines on the plexiglass plate, the present invention is a unit grid of 5 mm × 5 mm, and calculate the vertical projected area of the sample after melting by using the differential method + cutting and complementing method.
[0025] 2) Sample preparation: the present invention selects the calcium ash at the sintering production site as a flux, and dries the calcium ash and the iron ore powder sample to be tested at a temperature of 105° C. for 2 hours; the dried calcium ash and iron ore Grind the powder, pass through a -200 mesh process sieve, and take the under-sieve to test CaO and SiO 2 quality score.
[0026] 3) Sample preparation: on the premise of the actual value of the CaO mass fraction in the sinter or a certain fixed value, set the CaO mass fraction in the mixture as a constant amount, and according to the calcium ash and iro...
PUM
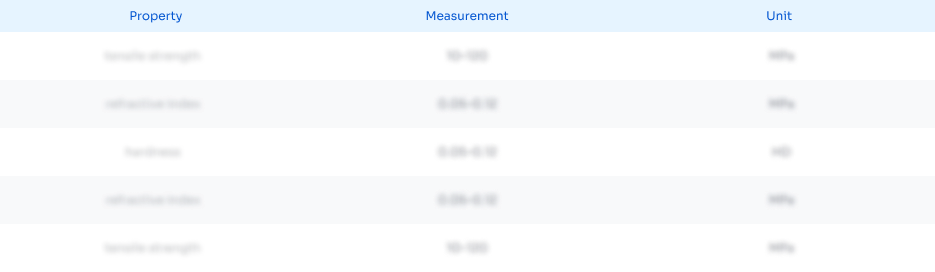
Abstract
Description
Claims
Application Information

- Generate Ideas
- Intellectual Property
- Life Sciences
- Materials
- Tech Scout
- Unparalleled Data Quality
- Higher Quality Content
- 60% Fewer Hallucinations
Browse by: Latest US Patents, China's latest patents, Technical Efficacy Thesaurus, Application Domain, Technology Topic, Popular Technical Reports.
© 2025 PatSnap. All rights reserved.Legal|Privacy policy|Modern Slavery Act Transparency Statement|Sitemap|About US| Contact US: help@patsnap.com