Cement clinker shock cooling process adopting material layer self-protection technology
A cement clinker and self-protection technology, applied in the field of cement clinker quenching, can solve the problems of low thermal efficiency, limited quenching area, unsatisfactory heat recovery effect, etc., and achieve the effect of improving clinker quality and ensuring cooling effect
- Summary
- Abstract
- Description
- Claims
- Application Information
AI Technical Summary
Problems solved by technology
Method used
Examples
Embodiment 1
[0051] An embodiment provided by the present invention: a cement clinker quenching process using material layer self-protection technology, the main body of the grate cooler:
[0052] Remove the old third-generation machine NC39325 and replace it with the fourth-generation grate cooler of LANE08-14a;
[0053] Equipped with the new fourth-generation grate cooler hydraulic station (purpose: to control the reciprocating motion of the hydraulic cylinders of various parts through the high-pressure pump and proportional valve of the hydraulic station to realize the number of reciprocating grate beds) and electric control cabinet;
[0054] Equipped with a new dry oil centralized lubrication device (purpose: the dry oil passes through the output oil pump and distributor to lubricate the movable support of each hydraulic cylinder of the grate cooler and the walking wheel bearings of each part of the grate bed) and the electric control cabinet;
[0055] Newly purchased 8 sets of 150 air...
Embodiment 2
[0079] An embodiment provided by the present invention: a cement clinker quenching process using material layer self-protection technology, performance guarantee conditions:
[0080] The temperature of the clinker entering the grate cooler: 1300-1400°C;
[0081] Clinker vertical weight: 1200—1300g / L;
[0082] Clinker output is below the rated output of grate cooler 6000tpd;
[0083] Kiln clinker particle size: the proportion of more than 25mm is less than 20%,
[0084] The proportion of less than 5mm is less than 30%;
[0085] Measurement of the clinker temperature of the grate cooler:
[0086] Screen and measure the round clinker particles below 25mm before crushing, and the particles exceeding 25mm shall not exceed 10%;
[0087] Adopt water-cooling method to carry out the measurement of clinker temperature, get the average value of measurement;
[0088] Operating air volume ≥ l.90Nm3 / kg.cl;
[0089] If the above conditions cannot be met, the clinker temperature of the ...
Embodiment 3
[0093] An embodiment provided by the present invention: a cement clinker quenching process using material layer self-protection technology, the specifications of main parts include:
[0094] Internal steel structure of shell and fixed grate bed: Quantity: 1 set, including: upper and lower shells and internal steel structure of fixed grate bed.
[0095] Movable grate baskets: 1 set, the first air chamber and the last air chamber adopt high-resistance grate plates.
[0096] Fixed grate plate, longitudinal seal, transverse seal.
[0097] The fixed grate adopts a new type of high-resistance grate, and the angle of the fixed bed is designed at 12°.
[0098] Active stringers: 8 sets.
[0099] Supporting device: guide wheel device: 1 set, supporting wheel device: 1 set.
[0100] Transmission device: 1 set, including: 8 displacement sensors;
[0101] The hydraulic transmission system consists of one section, the system rated working pressure: 181Pa, including: axial piston pump, q...
PUM
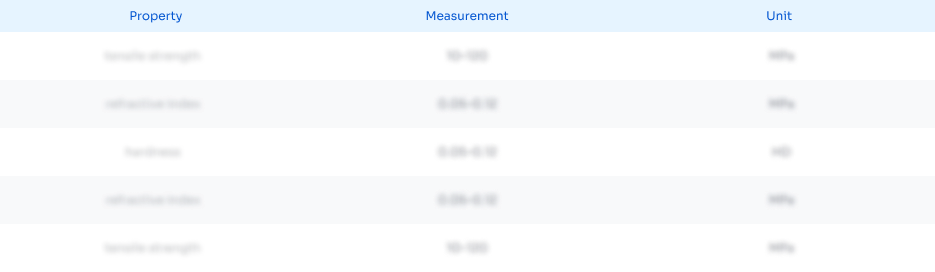
Abstract
Description
Claims
Application Information

- R&D
- Intellectual Property
- Life Sciences
- Materials
- Tech Scout
- Unparalleled Data Quality
- Higher Quality Content
- 60% Fewer Hallucinations
Browse by: Latest US Patents, China's latest patents, Technical Efficacy Thesaurus, Application Domain, Technology Topic, Popular Technical Reports.
© 2025 PatSnap. All rights reserved.Legal|Privacy policy|Modern Slavery Act Transparency Statement|Sitemap|About US| Contact US: help@patsnap.com