High-frequency vibration robot grinding device and tool self-compensation method for parts that are difficult to grind in narrow spaces
A narrow space, high-frequency vibration technology, applied in the direction of grinding drive device, grinding machine parts, workpiece feed movement control, etc., can solve the problem of automation, low processing efficiency, low efficiency, high loss of grinding tools, etc. problem, to achieve the effect of novel device structure, simple device structure and anti-drop effect
- Summary
- Abstract
- Description
- Claims
- Application Information
AI Technical Summary
Problems solved by technology
Method used
Image
Examples
Embodiment 1
[0033] This embodiment provides a tool self-compensating high-frequency vibration robot grinding device for parts that are difficult to grind in a narrow space, including a device base plate 4, a lateral reciprocating mechanism, a grinding base plate 22, an automatic tool compensation mechanism, and a tool clamping mechanism; The reciprocating mechanism is connected to the front of the device base plate 4, and the transverse reciprocating mechanism is used to drive the grinding base plate 22 to perform lateral reciprocating movement on the front of the device base plate 4; the tool automatic compensation mechanism includes a pressure control cylinder 6 and a longitudinal fixing member fixed on the grinding base plate 22 , and a longitudinal slider that slides with the longitudinal fixture; the tool clamping mechanism includes a rear clamping plate 15, a front clamping plate 10, an adjustment plate 26 and a clamping cylinder 13; the rear clamping plate 15 is fixed on the longitud...
Embodiment 2
[0045] This embodiment provides a tool self-compensation method for parts that are difficult to grind in a narrow space, including the following steps:
[0046] S1, placing the tool in the tool slot 31 of the tool self-compensating high-frequency vibration robot grinding device for the above-mentioned difficult-to-grind narrow space parts;
[0047] S2, carry out offline automatic tool compensation:
[0048] Utilize the limit detection cylinder 21 to rotate the cantilever 19 to the bottom of the tool, and detect whether the tool is in the working position through the proximity sensor 17. If the position of the tool meets the working conditions, the limit detection cylinder 21 extends downward and rotates the cantilever 19 to the tool rear. Start the grinding work; if the position of the tool does not meet the working conditions, the pressure control cylinder 6 drives the tool clamping mechanism to lift up, and then the clamping cylinder 13 is released, and the tool is brought d...
PUM
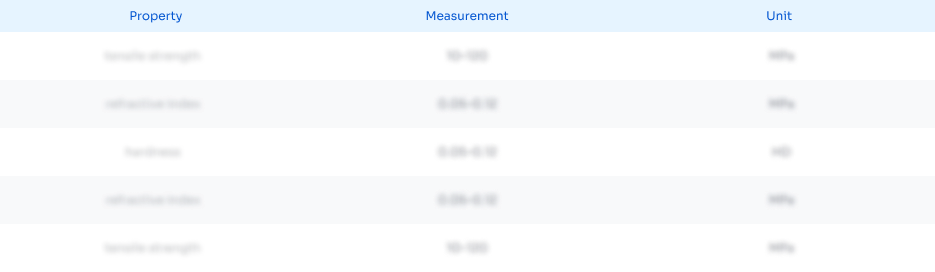
Abstract
Description
Claims
Application Information

- R&D
- Intellectual Property
- Life Sciences
- Materials
- Tech Scout
- Unparalleled Data Quality
- Higher Quality Content
- 60% Fewer Hallucinations
Browse by: Latest US Patents, China's latest patents, Technical Efficacy Thesaurus, Application Domain, Technology Topic, Popular Technical Reports.
© 2025 PatSnap. All rights reserved.Legal|Privacy policy|Modern Slavery Act Transparency Statement|Sitemap|About US| Contact US: help@patsnap.com