Ore grinding weak-magnetic strong-magnetic gravity separation reverse flotation process for magnetic hematite ore
An iron ore and reverse flotation technology, applied in flotation, magnetic separation, solid separation, etc., can solve the problems of low separation efficiency and complex process flow, and achieve the effect of shortening the beneficiation process, simple operation and low investment.
- Summary
- Abstract
- Description
- Claims
- Application Information
AI Technical Summary
Problems solved by technology
Method used
Image
Examples
Embodiment 1
[0034] The maghemite ore with an iron grade of 29.25% and a magnetite distribution rate of 79.02% was selected as the raw material. Grinding-weak magnetic field-strong magnetic field-gravity separation-reverse flotation process sorting, according to the following steps
[0035] Step 1. One-stage closed-circuit grinding and grading
[0036] After the primary maghemite ore is crushed, it is sent to a section of closed-circuit grinding and grading operation, and the fineness of the first-stage grading overflow product is controlled to be kept at -200 mesh, accounting for 70%;
[0037] Step 2, weak magnetic separation
[0038] A section of graded overflow product was fed into a weak magnetic separator with a magnetic induction intensity of 0.1 T for wet weak magnetic separation. Under the conditions of a pulp concentration of 33.33% and an ore feeding speed of 100 mL / s, weak magnetic concentrate and weak magnetic magnetic tailings;
[0039] Step 3, strong magnetic separation
...
Embodiment 2
[0053] Method is with embodiment 1, and difference is:
[0054] (1) Select maghemite ore with iron grade of 31.29% and magnetite distribution rate of 75.52% as raw material;
[0055] (2) The pulp concentration of wet weak magnetic separation is 35%, and the ore feeding speed is 120 mL / s;
[0056] (3) In the strong magnetic separation process, the background magnetic induction of the wet vertical ring strong magnetic machine is 0.7 T;
[0057] (4) When the coarse-grained products of the mixed magnetic concentrate are fed into the spiral chute of gravity separation after being coarsely and subdivided by the hydrocyclone, the feeding concentration is 12%;
[0058] (5) When the re-selected tailings are fed into the second-stage mill for grinding, the fineness of the second-stage grinding product is controlled, and it is ground to -200 mesh content accounting for 85%.
[0059] By adopting the technological process of the present invention, the final concentrate product obtained b...
Embodiment 3
[0061]Method is with embodiment 1, and difference is:
[0062] (1) Select maghemite ore with iron grade of 38.68% and magnetite distribution rate of 76.08% as raw material;
[0063] (2) The pulp concentration of wet weak magnetic separation is 37%, and the ore feeding speed is 180 mL / s;
[0064] (3) In the strong magnetic separation process, the background magnetic induction of the wet vertical ring strong magnetic machine is 0.8 T;
[0065] (4) When the coarse-grained products of the mixed magnetic concentrate are fed into the spiral chute of re-selection after being coarsely and subdivided by the hydrocyclone, the feeding concentration is 13%;
[0066] (5) When the re-selected tailings are fed into the second-stage mill for grinding, the fineness of the second-stage grinding product is controlled, and it is ground to -200 mesh content accounting for 88%.
[0067] By adopting the technological process of the present invention, the final concentrate product obtained by benef...
PUM
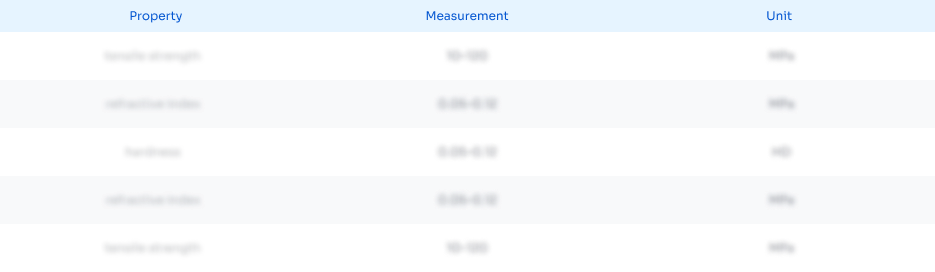
Abstract
Description
Claims
Application Information

- R&D
- Intellectual Property
- Life Sciences
- Materials
- Tech Scout
- Unparalleled Data Quality
- Higher Quality Content
- 60% Fewer Hallucinations
Browse by: Latest US Patents, China's latest patents, Technical Efficacy Thesaurus, Application Domain, Technology Topic, Popular Technical Reports.
© 2025 PatSnap. All rights reserved.Legal|Privacy policy|Modern Slavery Act Transparency Statement|Sitemap|About US| Contact US: help@patsnap.com