The manufacturing method of a LTCC heat sink
A manufacturing method and technology for heat sinks, which are applied to semiconductor/solid-state device parts, semiconductor devices, electrical components, etc., can solve the problems of increasing device volume, incompatible processes, and high production complexity, and achieve a simple and implementable manufacturing process. Strong performance and enhanced heat dissipation effect
- Summary
- Abstract
- Description
- Claims
- Application Information
AI Technical Summary
Problems solved by technology
Method used
Examples
Embodiment 1
[0015] The LTCC heat sink structure described in this embodiment is widely used in high-power LTCC modules. The integrated manufacturing of the LTCC heat dissipation function circuit is used as the whole single-chip LTCC module for heat dissipation of the entire LTCC module. This embodiment is a coplanar structure. For the LTCC heat sink, the P and N materials form a P and N coplanar structure on the same layer of LTCC film. The PN material is connected in series, and the galvanic couple composed of N-type and P-type thermoelectric materials works with an external DC power supply. The heat sink exists in the form of a galvanic couple, which is manufactured by the methods of paste printing, stack embedding, and low temperature co-firing compatible with the LTCC process. Printing, through-hole filling, low temperature co-firing process for built-in leads.
[0016] Taking the bismuth telluride thermoelectric material as an example, the bismuth telluride powder was obtained by th...
Embodiment 2
[0027] The LTCC heat sink in this experimental example is a single-piece LTCC heat sink, which can place high-power integrated circuits and high-power devices that need heat dissipation above the LTCC ceramic layer to achieve heat dissipation for devices and circuits. The galvanic couple composed of N-type and P-type thermoelectric materials works with an external DC power supply. The heat sink exists in the form of a galvanic couple, which is manufactured by the methods of paste printing, stack embedding, and low temperature co-firing compatible with the LTCC process. Printing, through-hole filling, low temperature co-firing process for built-in leads.
[0028] In this embodiment, the bismuth telluride thermoelectric material is taken as an example, and the bismuth telluride powder is obtained by the method of bulk bismuth telluride sputtering, and the LTCC heat sink is manufactured. The LTCC ceramic powder material is DuPont-943 produced by DuPont Company. The specific step...
PUM
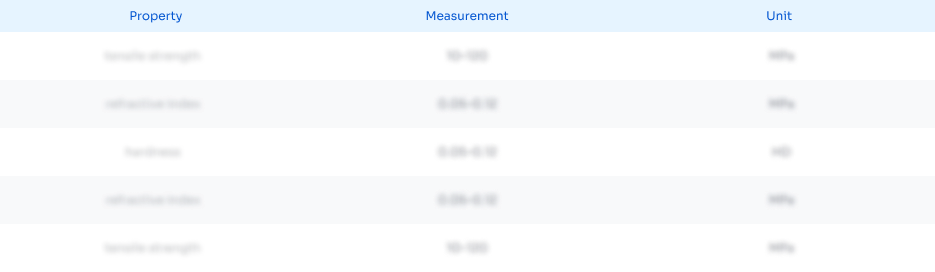
Abstract
Description
Claims
Application Information

- R&D
- Intellectual Property
- Life Sciences
- Materials
- Tech Scout
- Unparalleled Data Quality
- Higher Quality Content
- 60% Fewer Hallucinations
Browse by: Latest US Patents, China's latest patents, Technical Efficacy Thesaurus, Application Domain, Technology Topic, Popular Technical Reports.
© 2025 PatSnap. All rights reserved.Legal|Privacy policy|Modern Slavery Act Transparency Statement|Sitemap|About US| Contact US: help@patsnap.com