Pre-oxidation furnace for carbon fiber production
A pre-oxidation furnace and carbon fiber technology, applied in the fields of fiber chemical characteristics, textiles and papermaking, etc., can solve the problems of increased hot air resistance of tow knots, inconsistent speed of tow travel, and increased production hazards, etc.
- Summary
- Abstract
- Description
- Claims
- Application Information
AI Technical Summary
Problems solved by technology
Method used
Image
Examples
Embodiment Construction
[0018] The following will clearly and completely describe the technical solutions in the embodiments of the present invention with reference to the accompanying drawings in the embodiments of the present invention. Obviously, the described embodiments are only some, not all, embodiments of the present invention. Based on the embodiments of the present invention, all other embodiments obtained by persons of ordinary skill in the art without making creative efforts belong to the protection scope of the present invention.
[0019] see Figure 1-4 , a pre-oxidation furnace for carbon fiber production, comprising an overcoat 1, a tow 11, a blower 13 and a heater 14, the top of the inner cavity of the overcoat 1 is provided with an air intake hole 12, and the air intake hole 12 communicates with the blower 13 through a conduit, and the blower 13 communicates with the heater 14 through the conduit, and the lining tube 3 is fixedly installed on the left side wall of the jacket 1, and ...
PUM
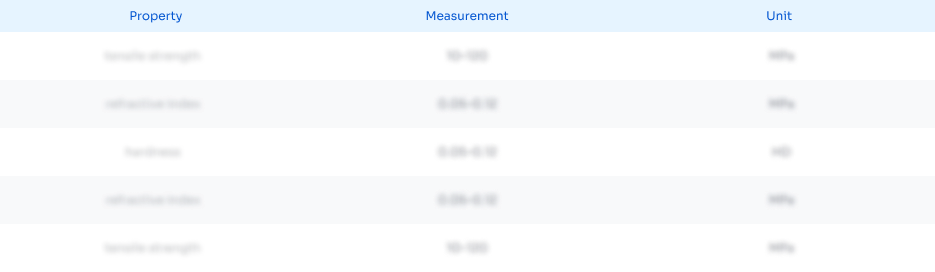
Abstract
Description
Claims
Application Information

- R&D
- Intellectual Property
- Life Sciences
- Materials
- Tech Scout
- Unparalleled Data Quality
- Higher Quality Content
- 60% Fewer Hallucinations
Browse by: Latest US Patents, China's latest patents, Technical Efficacy Thesaurus, Application Domain, Technology Topic, Popular Technical Reports.
© 2025 PatSnap. All rights reserved.Legal|Privacy policy|Modern Slavery Act Transparency Statement|Sitemap|About US| Contact US: help@patsnap.com